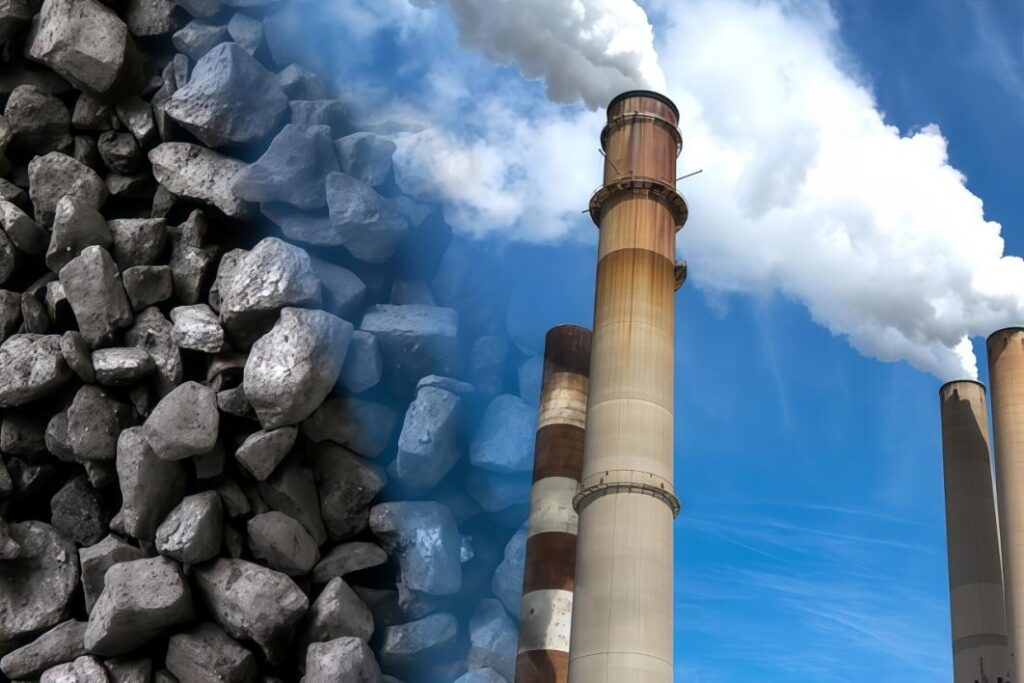
Coal-fired boilers burn coal to produce steam and power turbines. Yet incomplete combustion leaves carbon monoxide (CO) behind. A CO analyzer spots even small CO levels in the flue gas. This real-time data highlights fuel-rich zones and guides air adjustments. Consequently, CO analyzer help coal-fired power plants to optimize combustion, reduce emission, enhance safety, and achieve better operation and regulatory report.
How Do Carbon Monoxide (CO) Analyzers Boost Combustion Efficiency in Coal-Fired Power Plants?
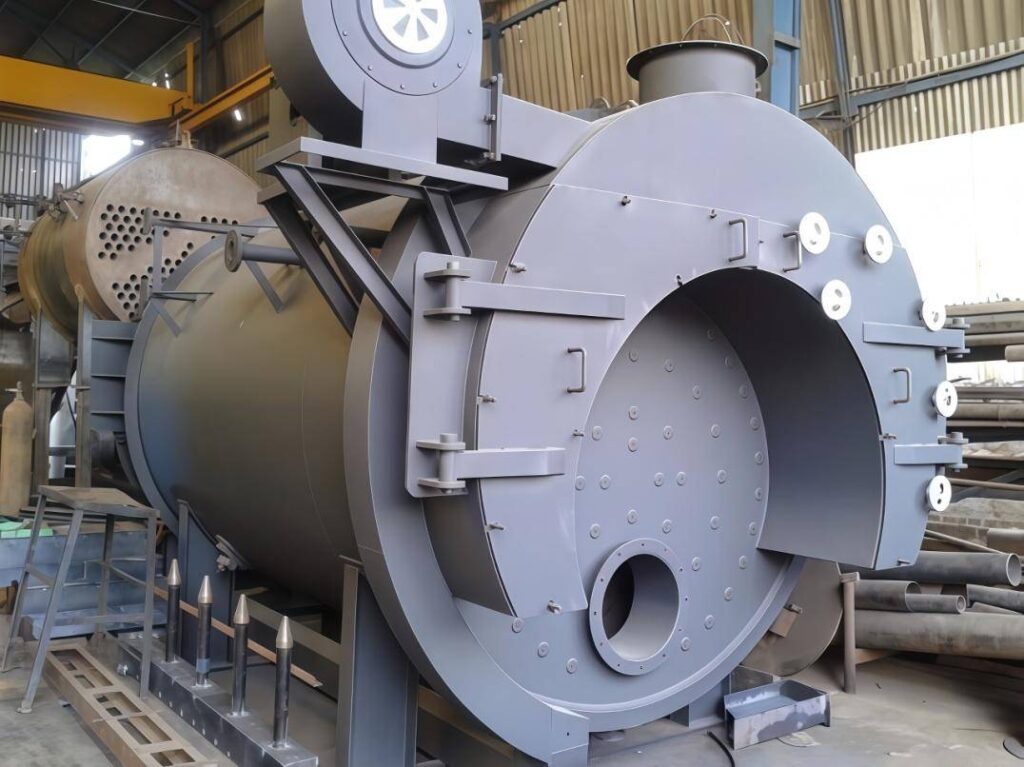
Coal-fired boilers depend on the perfect balance between air and fuel. Yet too much air wastes heat, while too little causes unburned coal and soot. Carbon monoxide analyzers act like precision gauges in this dance, which offering a direct measure of combustion quality.
By continuously monitoring CO levels, operators fine-tune the air–fuel ratio—reducing excess air and maximizing boiler efficiency and heat rate simultaneously. Reducing excess air by just 0.5% with CO data saves fuel and improves the heat rate under different loads.
Moreover, CO monitoring also helps curb NOₓ emissions. When plants run with unnecessary oxygen, flue gas carries more nitrogen into high-temperature zones, which breeds thermal NOₓ.
By targeting CO levels instead of relying on O₂ alone, operators avoid excess air and keep NOₓ in check. Plus, CO spikes act like bright warning flags pointing to “dirty” combustion pockets. These alerts prompt burner adjustments before soot buildup or flame stalls occur.
Why Are Carbon Monoxide (CO) Analyzers Critical for Safety?
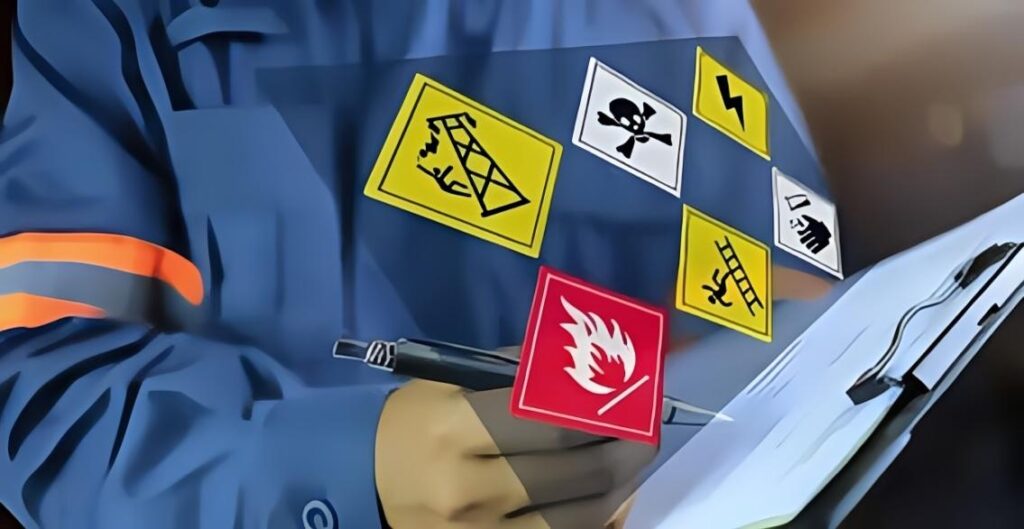
Coal-fired boilers demand constant vigilance when it comes to safety. Carbon monoxide analyzers serve as frontline alarms, alerting operators to emerging hazards so they can act before danger strikes.
Flame Stability Monitoring
A sudden rise in flue gas CO often signals flame instability or an imminent flame-out. By setting alarms based on CO thresholds, plants gain early warning. Consequently, operators can quickly boost secondary air or initiate fuel shutoff, preventing unsafe conditions from escalating.
Furthermore, advanced systems can trigger interlocks automatically—ensuring safety even when operator reaction lags. This proactive control keeps both crew and equipment safe.
Coal Carryover & Burner Fouling
Unexpected CO spikes also point to coal carryover—when raw fuel bypasses combustion—or burner fouling. Both situations can lead to soot buildup, slagging, or even fires.
CO detection lets maintenance staffs intervene swiftly:
- Inspect burner nozzles,
- Clear fouled passages,
- Adjust fuel/air settings.
Through these actions, CO monitoring transforms reactive fixes into planned, cost-effective maintenance.
Workplace & Environmental Safety
While most flue gas CO vents to the stack, CO monitoring ensures combustion remains complete. If CO climbs above design levels, systems can activate interlocks or trigger alarms for plant teams. This avoids harmful emissions and protects nearby communities.
In addition, CO monitors support EHS protocols by:
- Measuring workplace air quality,
- Validating combustion efficiency,
- Backing up compliance records with reliable data.
In essence, a CO analyzer shields both your plant and its people—keeping operations safe, compliant, and resilient.
Which Features Matter When Selecting a Carbon Monoxide (CO) Analyzer for Coal-Fired Plants?
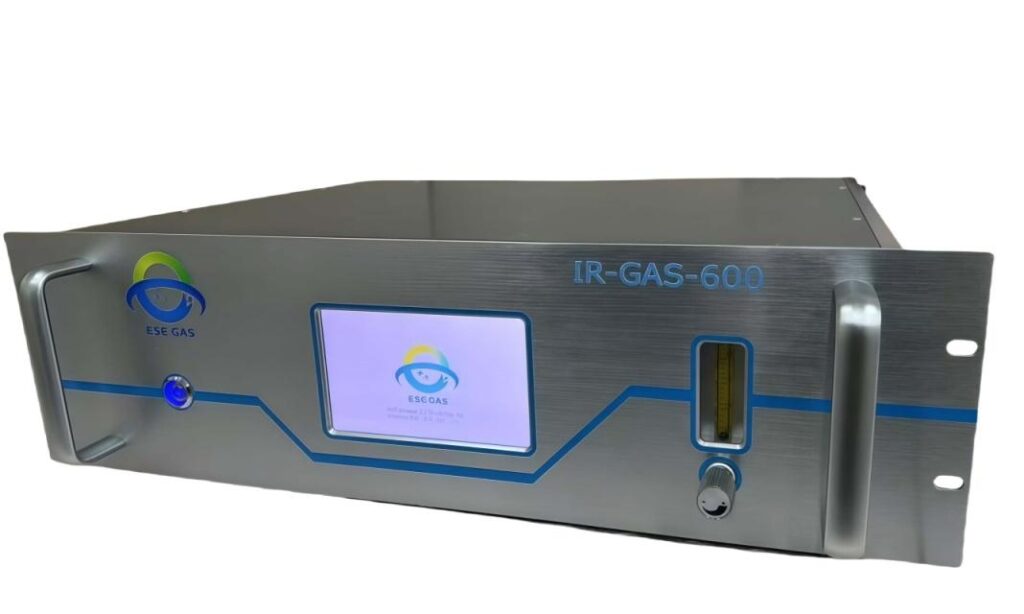
Selecting the right carbon monoxide (CO) analyzer is crucial for safe and efficient boiler operation. Here are the key features to focus on:
1. Detection Technology
- TDLAS (Tunable Diode Laser Absorption Spectroscopy) delivers ppm-level precision and fast response times. Although it is ideal for in-stack measurement, it comes at a premium and demands regular calibration
- NDIR (Non-Dispersive Infrared) is proven, sturdy, and cost-effective for flue-gas environments. Yet, it requires extractive sampling and periodic recalibration.
2. Measurement Range & Accuracy
Coal-boiler flue gas typically shows CO levels around 10–200 ppm, spiking higher during issues. An analyzer with ±10–20 ppm accuracy ensures early detection and tight combustion control. For mills or abnormal conditions, consider a broader range. Referencing full-span measurement avoids oversights.
3. Sampling Method
- Portable CO analyzers or CO analyzers in CEMS use heated probes and lines (~200–250 °C) to prevent condensation and soot buildup. Look for blowback filters and hot sample blocks to clear particles.
- TDLAS-based CO analyzers avoid gas extraction but must tolerate high heat and fouling—trading convenience for durability.
4. Environmental Ruggedness
Flue gas is abrasive—filled with dust, moisture, SO₂, HCl. Choose hardened materials like stainless steel and Teflon. Ensure the analyzer features heated sampling lines, moisture traps, and robust particulate filters to maintain accuracy and longevity
5. Output & Integration Capabilities
To mesh with CEMS/DCS systems, the analyzer should offer:
- Analog signals: 4–20 mA or 0–10 V
- Digitals: Modbus or Ethernet
- Fault relays and remote diagnostics
Also, check power demands and housing size for CEMS shelters.
A precise, business-ready carbon monoxide analyzer for coal plants should combine rugged construction, accurate detection, seamless integration, and resilience. Proper selection upfront pays dividends in reliability, compliance, and operational excellence.
How Can You Integrate Carbon Monoxide (CO) Analyzers with Your CEMS?
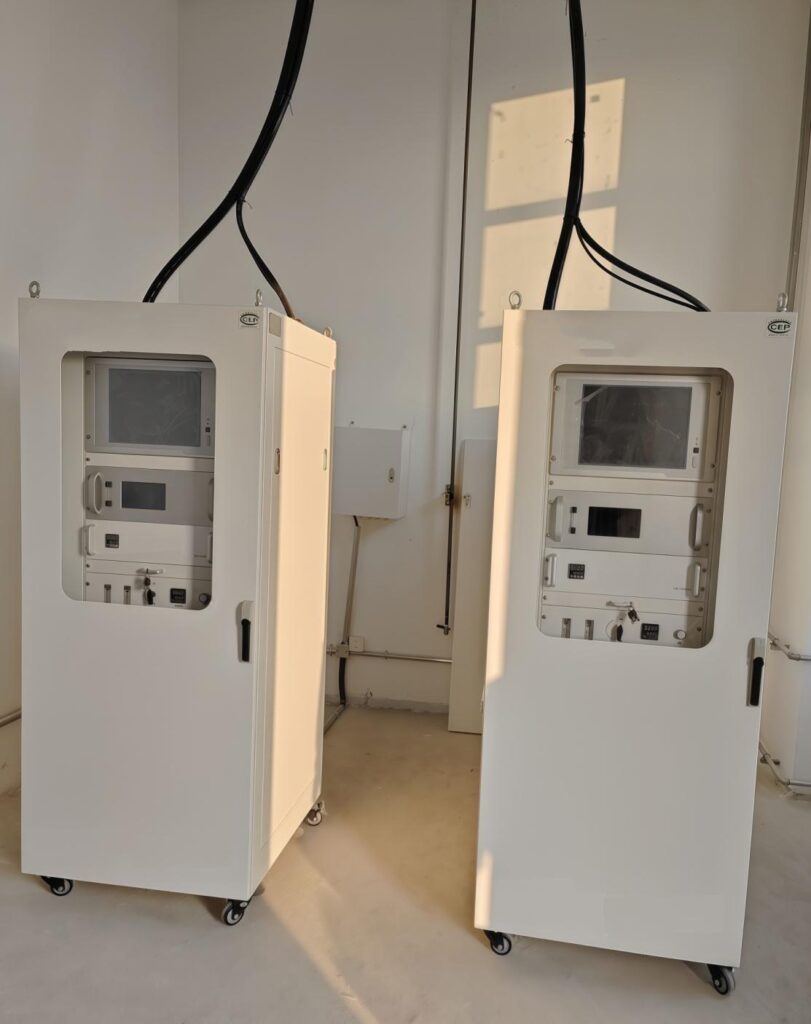
(CEMS)
Integrating carbon monoxide (CO) analyzers into your Continuous Emissions Monitoring System (CEMS) ensures cleaner, safer, and compliant plant operation. Here’s how to do it well:
1. Combine with Existing Multi-Gas CEMS
- Shared sampling setup: CO can piggy-back on your O₂, NOₓ, and SO₂ sample train via parallel piping.
- Flexible probe placement: Use a stack-based probe for compliance or deploy multiple in-furnace probes for combustion tuning.
- Common challenge: All setups need heated sample handling to prevent condensation and protect the analyzer
2. Robust Sampling & Conditioning
- Heated probe & lines: Maintain ~250 °C to avoid moisture and particulate buildup.
- Particulate filters + moisture traps: Coolers or dryers prepare gas before it reaches the analyzer.
- Sample pump: Ensures steady gas flow. Place the CO analyzer downstream of all conditioning equipment.
3. Seamless Data Acquisition
- Output signals: CO analyzers usually offer 4–20 mA, 0–10 V, and digital protocols like Modbus or Ethernet.
- Integration: Feed these signals into your CEMS/DCS controller, enabling trending, regulation triggers, and even burner control loops.
- Alarms & automation: Set thresholds for CO; exceeding limits triggers alerts or even safety actions.
4. Calibration Gas Integration
To meet compliance and ensure accuracy:
- Full path verification: Inject zero and span gases at the probe, not just at the analyzer, so the entire sample train is tested.
- Follow regulatory schedules: For example, EPA Part 60 and 75 require daily zero/span checks and quarterly linearity audits.
- Span levels: Use 50–100 % of analyzer range for Part 60, and 80–100 % for Part 75. Trigger failures on >10% deviation—ensuring immediate operator attention.
Why Integration Matters
Proper integration transforms carbon monoxide analyzers from standalone sensors into critical safety and combustion control tools. With good sample conditioning, reliable data flow, and consistent calibration, CO readings become actionable—safeguarding efficiency, compliance, and plant personnel.
Conclusion
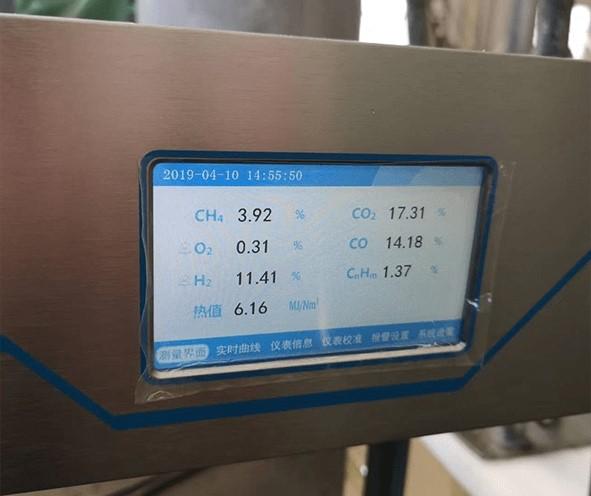
When you select a robust carbon monoxide analyzer, integrate it properly, and maintain it diligently, CO monitoring transforms into a powerful tool. It optimizes combustion, boosts safety, and underpins compliance. More than a sensor, CO monitoring becomes part of your plant’s operational backbone—driving smarter decisions and supporting sustainable, efficient operations.
In short: do it right and you’ll reap cleaner air, safer workers, and real bottom-line savings. Choose ESEGAS, your gas monitoring expert!