Ammonia is a widely used chemical in modern industrial production, especially in industries such as fertilizer production, refrigeration, and pharmaceuticals. While ammonia has important industrial applications, its volatility and toxicity also make it a potential environmental and health threat. Ammonia Escape refers to the leakage of ammonia gas into the environment during production, storage, or transportation. To ensure safe factory operation, protect employee health, and comply with environmental regulations, identifying and controlling Ammonia Escape has become a challenge that companies must face. In this process, gas analyzers play a key role. This blog will discuss in detail the importance and specific applications of gas analyzers in identifying Ammonia Escape.
What is Ammonia Escape and What Causes it?
Ammonia Escape refers to the phenomenon that in industrial processes containing ammonia, ammonia fails to participate in the reaction or be effectively collected as expected, but leaks from the system or is released into the environment. In detail, the reasons for ammonia escape mainly include the following aspects:
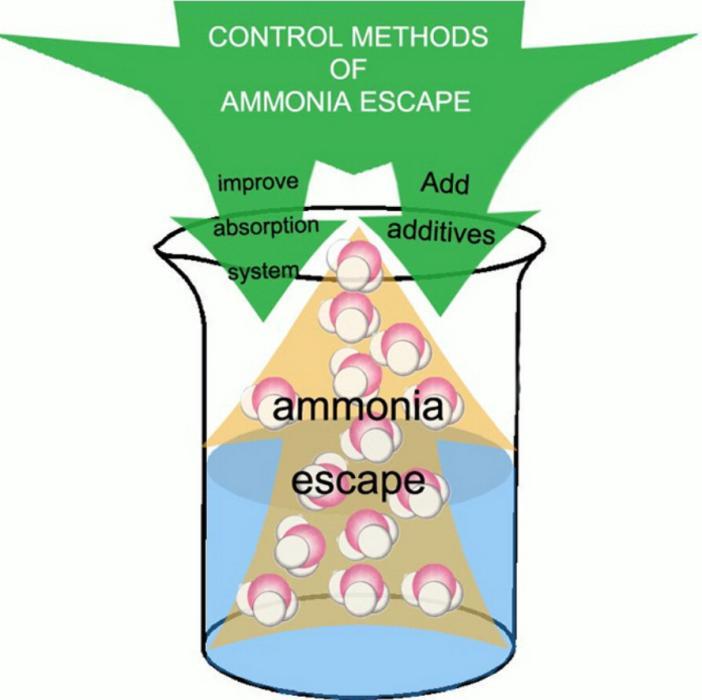
First, the use of ammonia spray guns is an important source of ammonia escape. The ammonia spray flow rate of each ammonia spray gun may be unevenly distributed, causing the local concentration of ammonia in the flue gas to be too high or too low. In addition, if the flow rate of flue gas is uneven, it will also affect the distribution of ammonia, making the ammonia concentration in some areas too high, increasing the possibility of ammonia escaping. Especially at the outlet of the spray gun, due to the difference in the amount of ammonia sprayed, ammonia escape is more likely to occur in places with high concentrations.
Secondly, reaction temperature is one of the key factors affecting ammonia escape. When the reaction temperature is too low, the reaction rate between NOx and ammonia will decrease, which will cause a large amount of NH₃ to escape from participating in the reaction. Conversely, if the reaction temperature is too high, ammonia may react with other substances to form undesirable by-products such as NO, which also increases the risk of ammonia escaping. Therefore, controlling the reaction temperature within an appropriate range is an important means to reduce ammonia escape.
In addition, the state of the catalyst will also affect ammonia escape. The clogging and aging of the catalyst will lead to a decrease in denitrification efficiency. To maintain environmental protection parameters within the standard range, it is necessary to increase the amount of ammonia injection. However, this often creates a vicious cycle: the clogging and aging of the catalyst requires more ammonia to participate in the reaction, and more ammonia may intensify the clogging and aging of the catalyst, causing more ammonia to escape.
The size of the atomized air volume will also affect the escape of ammonia. If the atomizing air volume is too small, the atomizing effect of the spray gun will be poor, resulting in the ammonia and flue gas not being fully mixed. This incomplete mixing will prevent part of the ammonia from participating in the reaction, resulting in ammonia escape.
Finally, the configuration of ammonia concentration is also an important factor affecting ammonia escape. If the ammonia concentration is improperly configured, too high or too low a concentration may cause ammonia to escape. A concentration that is too high may cause the ammonia to shut off during the spraying process, resulting in poor atomization and increased ammonia escape; while a concentration that is too low may require more ammonia to achieve the expected denitrification effect, which will also increase the risk of ammonia escape. risk.
The Dangers of Ammonia Escape
- Health Risks
Ammonia has significant effects on human health. Short-term exposure to high concentrations of ammonia can cause breathing difficulties, eye, and skin burns, and may even be fatal. Long-term exposure may cause chronic respiratory diseases and other health problems. Therefore, monitoring ammonia concentrations in the work environment is critical.
- Environmental Impact
Ammonia escape not only affects human health but also has a negative impact on the environment. Ammonia is one of the precursors of acid rain. It can react with moisture and other chemicals in the atmosphere to generate acid rain, destroying soil and water ecosystems. In addition, ammonia can also promote the formation of particulate matter (PM2.5) and affect air quality. (Image source: tiredearth)
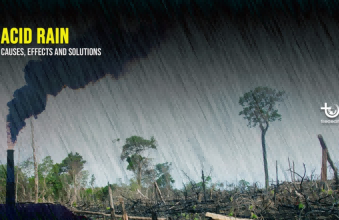
- Economic Losses
Ammonia escape can cause direct economic losses, including waste of raw materials and damage to equipment. What’s more, if environmental regulations are violated due to ammonia escape, companies may face high fines and production shutdowns, further increasing economic losses.
Ammonia escape will not only cause environmental pollution but may also be harmful to human health. Long-term exposure to ammonia may cause damage to the conjunctiva, nasal mucosa, lungs, skin, and other parts of the body, cause inflammation and ulcers, and even lead to chronic disease. Therefore, monitoring and controlling ammonia escape is crucial, and a series of measures need to be taken to reduce the occurrence of ammonia escape and protect the environment and human health.
Application of Gas Analyzer in Identifying Ammonia Escape
Gas analyzers are key tools in identifying Ammonia Escapes, with applications ranging from real-time monitoring to emergency response.The specific application of gas analyzers in identifying ammonia escape is discussed in detail below.
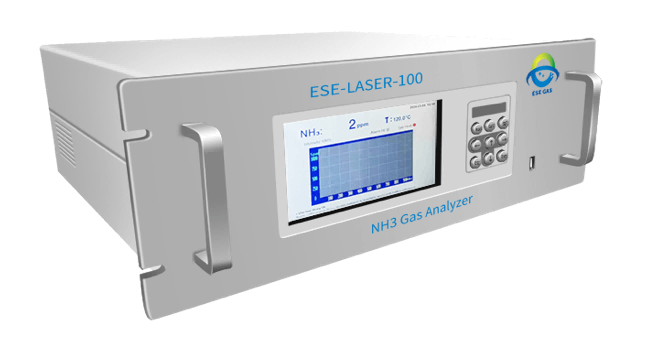
1. Online monitoring system
- Real-time monitoring of ammonia concentration
Online monitoring systems are an important part of companies’ efforts to prevent ammonia from escaping. By installing fixed gas analyzers in production areas, companies can monitor ammonia concentration changes in real-time. A typical online monitoring system includes a sensor network, data acquisition module, and central control system. Once the ammonia concentration exceeds the preset safety threshold, the system will immediately sound an alarm to notify the operator to take emergency measures.
- Case
A chemical plant installed multiple laser spectroscopic gas analyzers at key points on its production line. These analyzers can detect very low concentrations of ammonia and resist other interfering gases in the production environment. When a sensor detects that the ammonia concentration is close to the warning value, the system issues an alarm. By quickly locating the leak point, factory technicians repaired the leak in time and avoided a more serious safety accident.
2. Portable testing equipment
- Flexibility and convenience
Portable gas analyzers are suitable for on-site inspections and emergency detection due to their flexibility and convenience. This type of equipment is small in size, light in weight, easy to operate, and suitable for use in complex industrial environments. Portable analyzers typically have fast response times and high sensitivity, allowing operators to locate and identify ammonia leaks quickly.
- Application scenarios
During routine inspections, operators can use portable gas analyzers to inspect tanks, pipes, and valves. During the equipment maintenance process, the portable analyzer can detect ammonia residue on the disassembled equipment to ensure the safety of maintenance personnel. For example, maintenance personnel at a cold storage company will use a portable gas analyzer to check pipes and joints every time before performing equipment maintenance to ensure that there is no ammonia leakage.
3. Regular inspection and maintenance
- preventive maintenance
Although the online monitoring system provides real-time monitoring, regular comprehensive inspection and maintenance cannot be ignored. Enterprises should develop a regular testing plan and use gas analyzers to conduct comprehensive inspections of production facilities to identify potential leak risks. Through regular testing, small leaks caused by aging or damaged equipment can be discovered and preventive measures can be taken before the problem escalates into serious consequences.
- Maintenance case
A fertilizer plant conducts comprehensive ammonia leak detection every quarter. Technicians use portable laser spectrometers to inspect production lines, storage tanks, and delivery pipelines one by one. During an inspection, a trace amount of ammonia leakage was found in the sealing part of a storage tank. After timely repairs, possible major leakage accidents in the future were avoided.
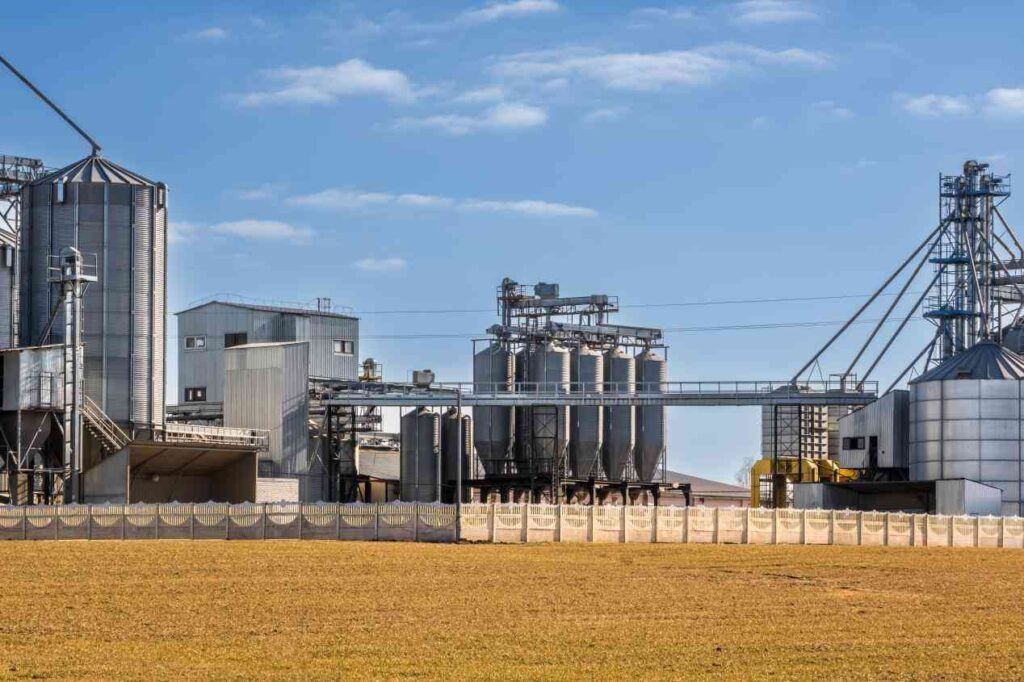
4. Data analysis and management
- Data recording and analysis
Modern gas analyzers usually have data recording and transmission functions and can upload detection data to the cloud or central control system in real-time. By analyzing historical data, companies can identify the patterns and trends of ammonia leaks, optimize production processes, and reduce the frequency of ammonia escapes.
- Intelligent management
Data analysis can also be used to evaluate the effectiveness of existing security measures and help companies improve security management strategies. Combining big data and artificial intelligence technology, enterprises can establish intelligent safety management systems to analyze possible risks in the production process in real-time, provide early warning and formulate corresponding countermeasures.
- case analysis
A large chemical company used historical data collected by a gas analyzer to discover that ammonia leaks occurred more frequently during a specific period. Through further analysis, technicians found that this period coincided with the high-load operation period of the equipment. Based on this discovery, the company adjusted its production plan, reduced high-load operating hours, and strengthened equipment maintenance, significantly reducing the frequency of ammonia leaks.
5. Emergency response
- Quick response mechanism
When an ammonia leak occurs, a gas analyzer can help companies quickly locate the leak point and evaluate the leak range and concentration. Portable gas analyzers are especially suitable for emergency response. They can provide instant ammonia concentration data at the accident site and help emergency personnel formulate scientific disposal plans.
- Emergency drills
Companies can use gas analyzers to conduct emergency drills, simulate ammonia leak accidents, and test and evaluate the effectiveness of emergency plans. For example, a chemical plant regularly organizes ammonia leak emergency drills and uses portable gas analyzers to detect simulated leak sources to ensure that emergency personnel are familiar with equipment operating procedures and improve emergency response capabilities.
6. Comprehensive application cases
- Comprehensive monitoring of fertilizer plants
A large fertilizer plant adopted a comprehensive gas monitoring solution, including a fixed online monitoring system and a portable gas analyzer. Multiple laser spectrometers are installed in the production area to monitor ammonia concentration in real time. At the same time, a portable analyzer is equipped for regular inspections and emergency testing. Through systematic monitoring and management, the factory has successfully reduced the risk of ammonia leakage and ensured employee health and environmental safety.
- Refrigeration industry applications
In the refrigeration industry, the widespread use of ammonia as a refrigerant increases the risk of ammonia leaks. A cold storage company has installed a fixed gas analyzer to monitor the ammonia concentration in the cold storage in real time, and is also equipped with a portable analyzer for daily inspection and emergency detection. During an equipment maintenance period, technicians used portable analyzers to quickly detect and repair a pipeline leak, avoiding the impact of ammonia leaks on production and the environment.
Through the above-detailed application scenario analysis, we can see the key role of gas analyzers in identifying ammonia escape. Whether it is real-time monitoring through online monitoring systems or flexible detection using portable equipment, gas analyzers provide enterprises with strong technical support to ensure production safety and environmental protection. In the future, with the continuous advancement of detection technology, the application of gas analyzers in ammonia escape identification will be more extensive and in-depth, providing a more solid guarantee for the safe production of enterprises.
Gas Analyzer Selection and Maintenance
1. Choose the right gas analyzer
Different types of gas analyzers have different advantages and disadvantages, and companies should choose the appropriate equipment according to their own needs. Laser spectrometers are ideal for situations where high-precision detection is required, while electrochemical sensors are also a good choice for situations where the budget is limited and environmental conditions are relatively stable.If you want to learn more about how to choose the right gas analyzer for you, you can read our blog!
2. Regular calibration and maintenance
The accuracy and stability of a gas analyzer depend on regular calibration and maintenance. Enterprises should develop detailed maintenance plans and regularly calibrate and inspect equipment to ensure that it is always in optimal working condition. Especially electrochemical sensors require frequent calibration because they are sensitive to environmental conditions.
3. Training and safety management
To give full play to the role of gas analyzers, companies also need to train operators to master the use of equipment and emergency response measures. In addition, enterprises should establish a sound safety management system and clarify the responsibilities of personnel at all levels to ensure that ammonia leaks can be responded to and dealt with quickly when an ammonia leak occurs. If you want to know more about the maintenance of gas analyzers, you can read our previous blogs!
Conclusion
Gas analyzers play an important role in identifying ammonia escape. They can help companies monitor ammonia concentration in real time, detect and deal with leakage problems promptly, and ensure production safety and employee health. At the same time, gas analyzers can also assist companies in optimizing production processes and reducing economic losses and environmental impacts. By choosing the right gas analyzer, performing regular maintenance, and training operators, companies can effectively control ammonia escape and improve overall safety management.
In the future, with the advancement of science and technology and the increasing awareness of environmental protection, the application of gas analyzers in industry will be more extensive and in-depth. Enterprises should actively adopt advanced gas detection technology, continuously improve safety management levels, and contribute to sustainable development. if you have any questions, please contact us directly!