Polysilicon production depends on invisible gases—get them wrong, and you risk low yield, poor quality, or even explosions. Real-time gas monitoring is not optional.
In polysilicon manufacturing, precise and continuous gas analysis is essential to ensure product purity, process safety, and cost efficiency. Advanced analyzers from companies like ESEGAS are critical in achieving these goals.
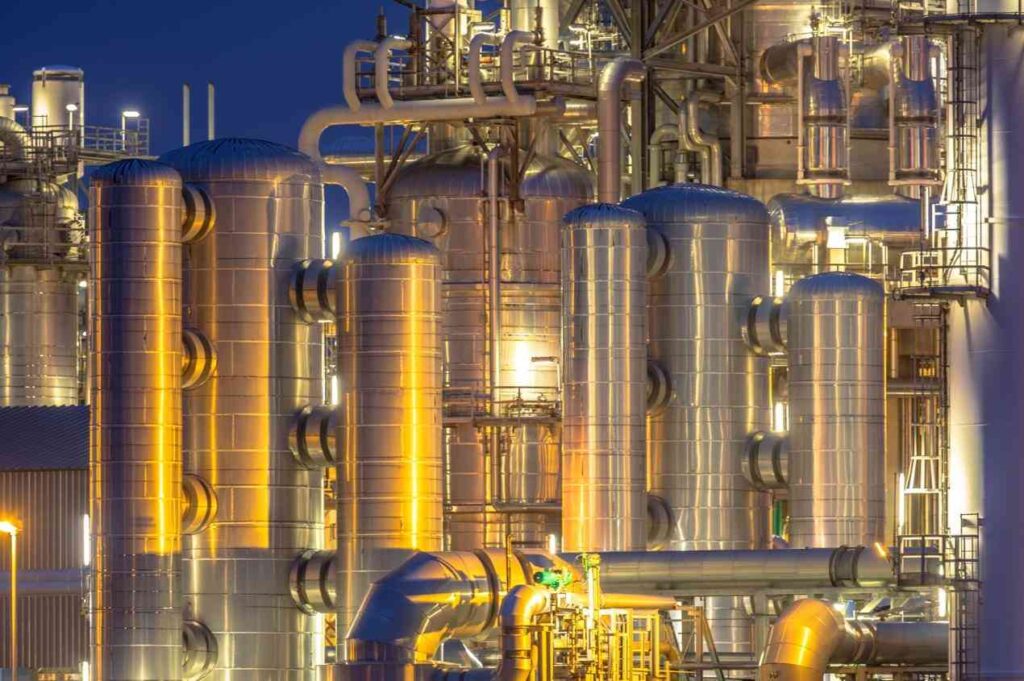
Even if you know process gas analyzers are important, understanding their specific applications in the polysilicon process—from safety to efficiency—will help you make smarter operational decisions.
Why is gas analysis essential in polysilicon production?
Unseen gas fluctuations silently erode efficiency and threaten safety—until failure strikes.
Polysilicon production involves high-temperature reactions with sensitive gas-phase chemistry. The processes—like the Siemens method or Fluidized Bed Reactor (FBR) technique—rely heavily on precise gas composition to ensure successful silicon deposition. Variations in the concentration of silane (SiH₄), hydrogen (H₂), or hydrochloric acid (HCl) can drastically affect product purity, deposition rate, and energy consumption.
Continuous gas monitoring with advanced analyzers, such as those from ESEGAS, ensures that each stage of the process stays within strict operating parameters. These analyzers provide real-time data on gas flow rates, concentrations, and purity levels, enabling plant operators to adjust conditions dynamically and prevent costly deviations.
For example, if the ratio of HCl to H₂ is not accurately maintained during the Siemens process, polysilicon rods may develop impurities or even fail to form. With ESEGAS analyzers in place, deviations can be detected within seconds, enabling closed-loop control that minimizes waste, maintains production uptime, and meets increasingly strict quality requirements.
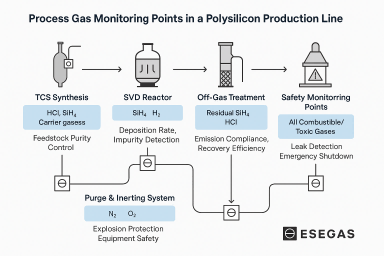
Beyond yield and quality, gas analyzers are also crucial for process optimization. Real-time data allow for fine-tuning of gas usage, helping manufacturers reduce raw material costs and environmental impact. This becomes especially important as the industry shifts toward more energy-efficient and sustainable silicon production.
Which gases do analyzers monitor during polysilicon production?
What you can’t measure, you can’t purify—undetected gas imbalances corrupt crystal quality and disrupt yield.
Gas analyzers in polysilicon manufacturing are vital for detecting specific process gases that influence both the reaction kinetics and product integrity. Each gas has a distinct role, and any variation in its concentration can impact the formation of high-purity polysilicon.
Here’s a breakdown of the main gases monitored:
- Silane (SiH₄): The primary silicon source in CVD, highly reactive and pyrophoric. Its concentration affects deposition rate and crystal uniformity.
- Hydrogen (H₂): Used as a carrier and process gas; its ratio with SiH₄ directly influences surface reactions and energy balance.
- Hydrochloric acid (HCl): Used in the Siemens process for the formation of trichlorosilane (TCS) and reactor cleaning; requires tight handling due to corrosive properties.
- Nitrogen (N₂): Used for purging and inerting systems; essential for explosion prevention.
- Oxygen (O₂): Often monitored as a contaminant; even trace levels can oxidize silicon surfaces or alter reaction pathways.
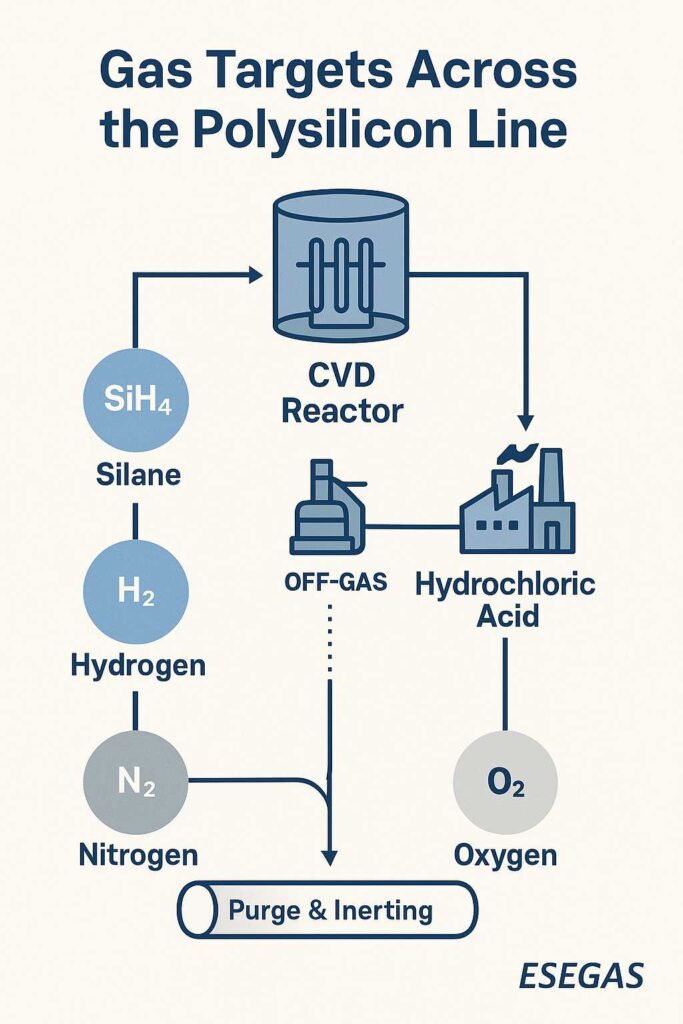
ESEGAS analyzers are equipped with real-time sensing technology that delivers accurate readings down to ppm levels, ensuring that every gas interaction is accounted for. This granular insight allows engineers to maintain optimal reaction conditions, reduce contamination, and meet rigorous industry specifications.
How is gas analysis used in CVD during polysilicon growth?
Uncontrolled gas flow in CVD doesn’t just reduce efficiency—it destroys crystal integrity.
Chemical Vapor Deposition (CVD) is the central process in polysilicon manufacturing, where high-purity silicon is deposited from gas-phase precursors like silane (SiH₄). In this highly sensitive step, even minor deviations in gas composition, pressure, or flow rate can cause defects, reduce deposition efficiency, or result in poor-quality silicon rods or granules.
Gas analysis during CVD is essential to stabilize deposition conditions, optimize reaction efficiency, and prevent contamination. Solutions from ESEGAS enable real-time process insight and automated control.
Key Roles of Gas Analysis in CVD:
- Monitoring Silane (SiH₄) and Hydrogen (H₂) Ratios
- SiH₄ is the source gas; H₂ often acts as a carrier or diluent.
- The ratio determines deposition rate, energy balance, and film uniformity.
- ESEGAS analyzers provide second-by-second readings to avoid over-deposition or inefficient usage.
- Contaminant Detection (e.g., O₂, H₂O)
- Even ppm-level oxygen or water vapor can oxidize the substrate or introduce defects.
- Real-time detection allows preemptive purging or system calibration.
- Pressure and Flow Verification
- CVD processes often operate under controlled vacuum or low pressure.
- Integrated sensors in ESEGAS systems ensure consistency in flow dynamics, preventing hot spots or dead zones.
- Exhaust Gas Analysis
- Post-reaction gases (e.g., unreacted SiH₄, byproducts) are monitored to assess process efficiency and ensure safe handling.
- This data supports closed-loop control and can inform when to adjust precursor input.
- System Health and Predictive Maintenance
- Trends in gas concentration or anomaly detection can indicate leaks, fouling, or degradation in gas lines or reactors.
- ESEGAS analyzers support smart diagnostics and integration into plant-wide control systems.
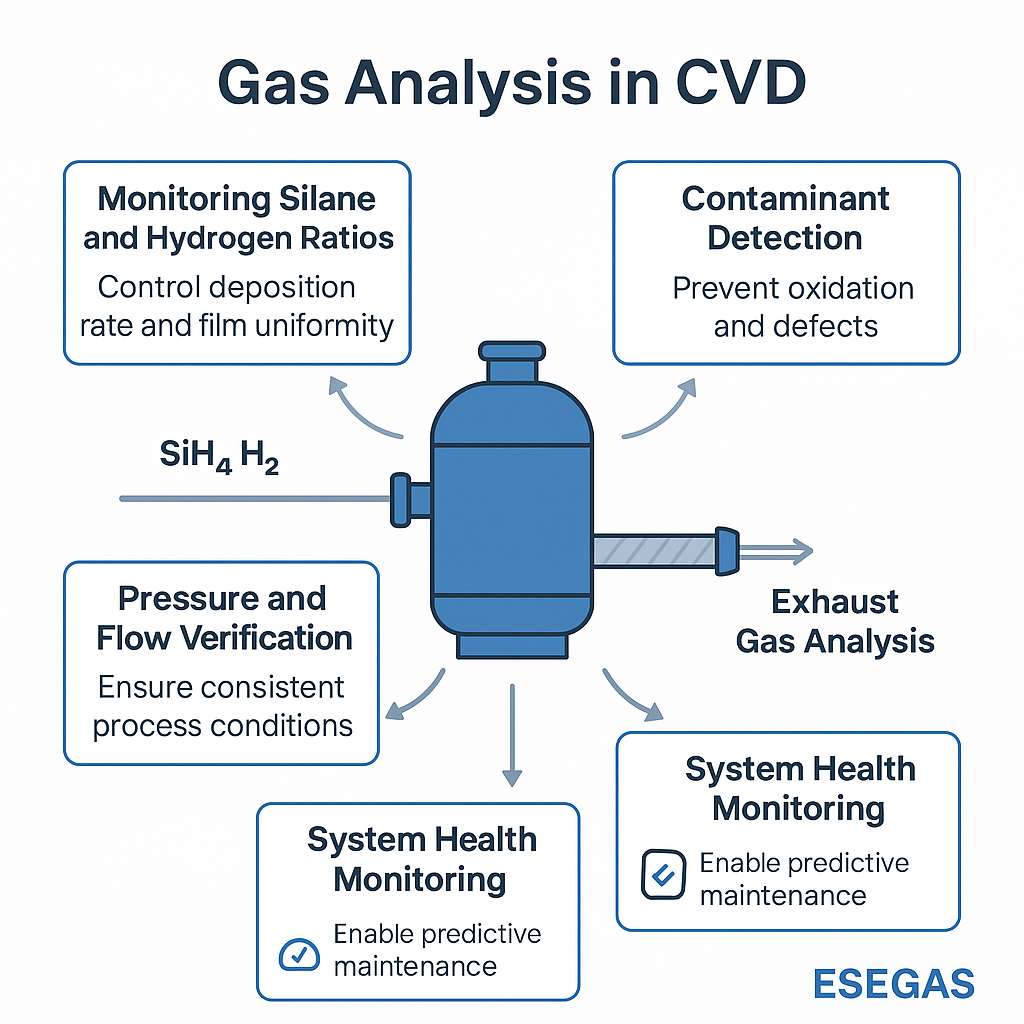
In CVD, real-time gas analysis—especially of SiH₄, H₂, and trace contaminants—is essential to maintain deposition quality, reduce waste, and enable automated process control. ESEGAS analyzers support precise, stable, and efficient silicon layer growth.
How do gas analyzers improve safety in polysilicon plants?
In polysilicon plants, safety issues don’t give warnings—gas leaks, explosions, or toxic exposure can happen in seconds.
The production of polysilicon involves hazardous gases such as silane (SiH₄), hydrogen (H₂), and hydrochloric acid (HCl), many of which are pyrophoric, toxic, or corrosive. Without continuous gas monitoring, even a small leak or imbalance can escalate into fire, explosion, or severe health hazards.
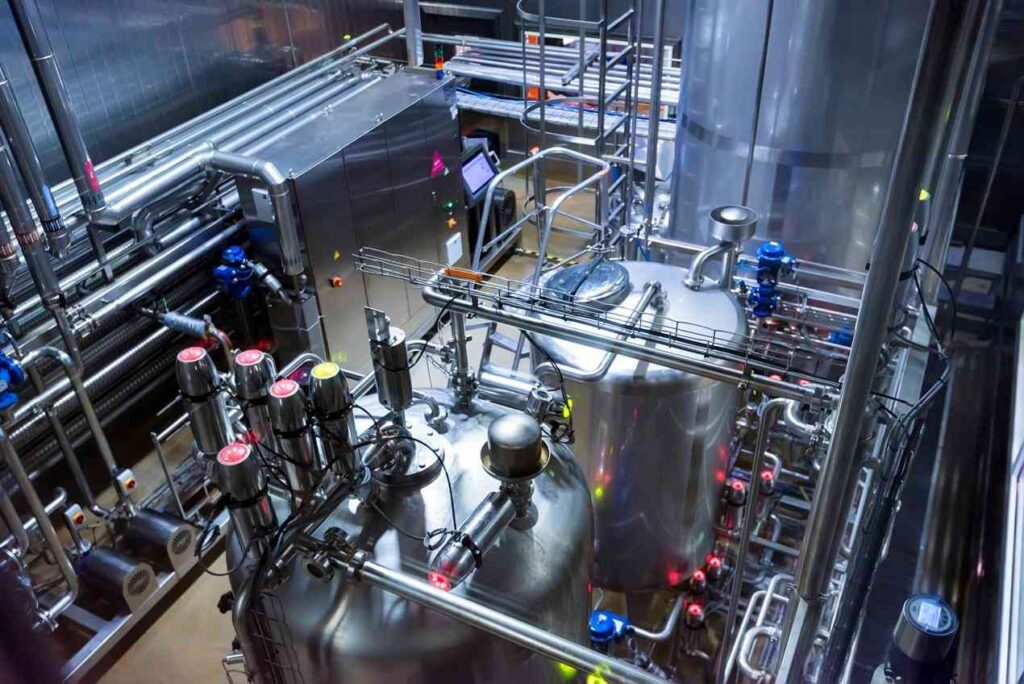
Gas analyzers play a critical role in plant safety by enabling real-time detection, early intervention, and system shutdown protocols. Solutions from ESEGAS provide precise, continuous protection across all safety-critical zones.
Key Ways Gas Analyzers Improve Safety:
- Leak Detection and Early Warning
- Gas analyzers continuously sample ambient air and process lines to detect leaks of SiH₄, H₂, or HCl.
- ESEGAS systems trigger real-time alarms when threshold levels are exceeded—often before human senses or standard detectors react.
- Explosion Prevention through Purge Control
- In CVD chambers or gas cabinets, improper purging can allow oxygen to mix with flammable gases.
- Analyzers verify nitrogen (N₂) or argon purging effectiveness and ensure that residual oxygen (O₂) is below explosive limits.
- Toxic Exposure Protection
- HCl is highly corrosive and harmful even at low concentrations.
- Continuous monitoring ensures operators are not exposed and that ventilation systems function effectively.
- Emergency Shutdown Integration
- ESEGAS analyzers can be linked directly to programmable logic controllers (PLCs) or distributed control systems (DCS).
- In case of abnormal readings, automatic safety protocols can shut off valves, isolate zones, and activate emergency exhaust.
- Post-Incident Diagnostics and Compliance
- Recorded gas data allows root cause analysis after any incident.
- It also supports compliance with safety regulations like OSHA, REACH, or China’s GB/T standards.
Snippet-ready summary:
Gas analyzers improve polysilicon plant safety by detecting leaks, preventing explosions, monitoring toxic exposures, and enabling automatic shutdowns. ESEGAS solutions offer real-time, high-precision protection in all critical areas.
What should manufacturers consider when selecting a gas analyzer?
Choosing the wrong analyzer isn’t just a bad investment—it can lead to product failure, safety risks, and regulatory violations.
In polysilicon production, the environment is extreme: high temperatures, corrosive gases, and the need for near-instantaneous accuracy. A gas analyzer that cannot meet these challenges consistently will compromise the entire production line.
To ensure reliability, safety, and long-term ROI, manufacturers must evaluate analyzers across performance, integration, and lifecycle factors. ESEGAS systems are built to meet these specific demands.
Key Selection Criteria for Gas Analyzers in Polysilicon Plants:
- Measurement Precision & Sensitivity
- Detection down to ppm or ppb levels is essential for gases like SiH₄ or O₂.
- ESEGAS analyzers are calibrated for high-resolution performance even in dynamic gas flows.
- Response Time (T90)
- In fast-changing processes like CVD or off-gas treatment, analyzers must respond in under 5–10 seconds.
- Delays could result in over-deposition, unsafe mixtures, or system lag.
- Material Compatibility & Durability
- Analyzer components must resist corrosion from HCl or TCS, and handle elevated temperatures.
- Look for analyzers with inert sample paths, temperature control, and anti-corrosive housings.
- Maintenance & Calibration Requirements
- Frequent manual recalibration reduces uptime and increases labor costs.
- ESEGAS systems support auto-calibration and predictive maintenance alerts to streamline upkeep.
- Integration with DCS / Safety Systems
- The analyzer should support Modbus, Profibus, or Ethernet for seamless integration with control infrastructure.
- In safety-critical zones, the ability to trigger interlocks or alarms automatically is essential.
- Regulatory & Quality Compliance
- Analyzers must align with ISO, SEMI, and national safety standards.
- Documentation and digital traceability are often required for audits.
- Total Cost of Ownership (TCO)
- Consider not just the purchase price but energy usage, consumables, sensor lifespan, and maintenance cycles.
- ESEGAS emphasizes long sensor life and minimal drift, helping lower TCO over 5–10 years.
When selecting a gas analyzer for polysilicon production, manufacturers should consider accuracy, response time, durability, system integration, and TCO. ESEGAS analyzers meet industry demands with precision, reliability, and safety-first design.