Gas analysis plays a vital role in environmental protection, industrial safety and production efficiency. Continuous Emission Monitoring System (CMES) is a key tool to ensure that gas emissions comply with regulations and standards. However, there are several factors that need to be considered when selecting a CMES system that suits your gas analysis needs. This article will show you how to choose the right CMES system for your needs.
Step 1: Clarify Needs and Goals
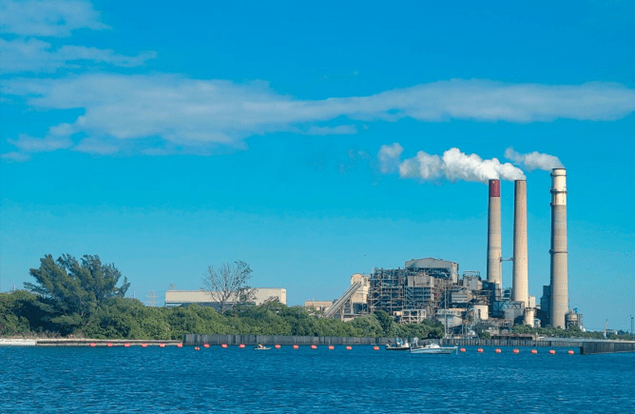
Before selecting the right CMES system for your gas analysis needs, the first priority is to clarify your needs and goals. Different industries and applications may have different needs. Here are some possible requirements:
- Regulatory Compliance: Ensure your gas emissions monitoring system complies with local, national and international regulations and standards.
- Precision and accuracy: Your application may require highly accurate gas concentration measurements, so choose a CMES system with high resolution and accuracy.
- Multi-gas monitoring:If you need to monitor multiple gases, make sure the system you choose offers this versatility.
- Data reporting and recording: You may need to generate detailed reports and records to meet regulatory or internal requirements.
- Long term monitoring: If continuous long-term monitoring is required, system stability and reliability will be critical.
Clarifying your needs and goals will help you better choose a suitable CMES system.
Part 2: Determine Process Parameters
When choosing CEMS, Process parameters is an important consideration as it must be able to accurately measure the gases and particles emitted from the process. The gas type, temperature and pressure of the process will determine the type of CEMS that should be used. For example, for processes involving highly reactive gases such as hydrogen sulfide, a CEMS with high temperature and high pressure capabilities may be required.
Additionally, where hazardous gases or particles are emitted, specialized CEMS may be required to measure these emissions.
CEMS must also be able to accurately measure and evaluate process operating parameters such as gas flow, temperature and pressure. This will ensure that the CEMS provides accurate measurements of process emissions. Additionally, CEMS must be able to operate in the environment in which they are used. This is important to ensure that the CEMS is not damaged or damaged by the process environment. Additionally, the CEMS must be able to operate over a wide range of temperatures and pressures to ensure it can accurately measure emissions from the process.
Step 3: Choose The Right Sensing Technology
At the heart of the CMES system is the sensing technology used to detect and measure gas emissions. Different gases require different sensing technologies. Here are some common sensing technologies:
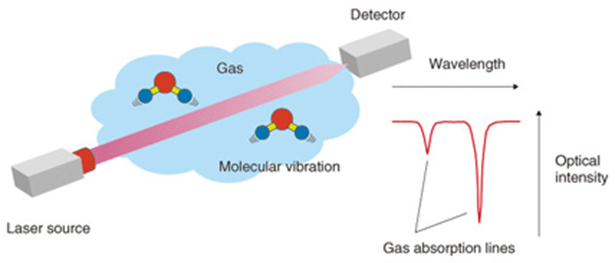
- Infrared sensor: It is suitable for measuring specific gases such as CO2 and CH4, with high accuracy and stability.
- UV sensor: It is suitable for measuring SO2, NO2 and other gases, but you need to pay attention to the absorption interference of the beam.
- Electrochemical sensors: Used to measure gases such as carbon monoxide (CO) and sulfur dioxide (SO2), but requires regular calibration.
- Laser absorption spectrum: Provides high precision and selectivity, suitable for multi-gas monitoring.
Choose the appropriate sensing technology based on your needs and gas type.
Below is a table outlining the differences between common gas sensing technologies:
Technology | Advantage | Shortcoming | Applicable Gas | Application Areas |
Infrared sensor | High precision | Affected by spectral interference | CO2, CH4 and other gases | Environmental monitoring, greenhouse gas emission monitoring |
UV sensor | High sensitivity | Need to eliminate beam absorption interference | SO2, NO2 and other gases | Air quality monitoring, industrial emission monitoring |
Electrochemical sensors | Suitable for a variety of gases | Requires regular calibration | CO, O2, NO2 and other gases | Industrial safety, indoor air quality monitoring |
Laser absorption spectrum | High precision and selectivity | Equipment cost is higher | Various gases | Precision measurement, scientific research applications |
Semiconductor sensor | Low cost and miniaturization | Sensitivity is affected by temperature and humidity | VOCs, CO, NH3 and other gases | Indoor air quality monitoring, personal safety equipment |
proton exchange membrane sensor | High selectivity, suitable for high temperature and high humidity environments | higher cost | H2, H2S, NH3 and other gases | Chemical plant, industrial emission monitoring |
Step 4: Data Quality and Calibration
When selecting a continuous emissions monitoring (CMES) system for your gas analysis needs, ensuring data quality and calibration is critical, as these factors directly impact the accuracy and trustworthiness of your monitoring data. The following is about Data quality and calibration Detailed discussion of:
- Data quality control
Data quality control is a key factor in ensuring that your CMES system provides high-quality, reliable data. Here are some key points on data quality control:
- Real-time monitoring and alarming: The CMES system should have real-time monitoring and alarm functions to immediately identify and respond to any data anomalies or equipment failures. This helps prevent the propagation of erroneous data while reducing uncertainty in subsequent analyses.
- Data correction and filtering:The system should provide data correction and filtering functions to remove potential noise and interference to ensure accurate measurement results.
- Calibration period:Determine how often the CMES system needs to be calibrated. Typically, periodic calibration is important to ensure system accuracy. The frequency of calibration may vary depending on gas type and environmental conditions.
- Data redundancy:By using multiple sensors or monitoring points, data redundancy can be improved and the impact of errors at a single point on the overall data can be reduced. This can increase system reliability.
- automatic calibration
Automatic calibration is a key factor in ensuring the stability and accuracy of CMES systems. Here are the key points about automatic calibration:
- Zero and span calibration: The system should have zero and span calibration capabilities to correct the sensor’s baseline and measurement range. This helps maintain system accuracy.
- Automatic calibration procedure:The system should be able to perform calibration procedures automatically without manual intervention. This reduces operational complexity and reduces operator errors.
- Calibration report:The system should generate calibration reports documenting the details of each calibration for subsequent review and verification.
- Calibration frequency:Determine the frequency of calibration and adjust it based on monitoring conditions and gas characteristics. Some gases may require more frequent calibrations, while others can be calibrated over a longer period of time.
- remote access
Remote access is a key factor in ensuring the monitoring and management of CMES system performance. Here are some key points about remote access:
- Remote monitoring: The CMES system should support remote monitoring capabilities, allowing you to track system performance in real time and detect problems in a timely manner.
- remote diagnosis:The system should provide remote diagnostic capabilities to help identify and resolve problems, thereby reducing downtime.
- Remote calibration:Some CMES systems support remote calibration, which can increase system availability without the need for on-site operations.
- Remote upgrade: The system should support remote upgrades to ensure that the system maintains the latest functionality and performance.
Data quality and calibration are key factors in ensuring your CMES system provides trustworthy, accurate data. By implementing real-time monitoring, data correction, and automatic calibration, you can minimize errors and increase data reliability. Remote access capabilities will help you monitor and manage your system in a timely manner, ensuring it remains high performing during extended monitoring periods.
Step 5: Consider The On-Site Environment
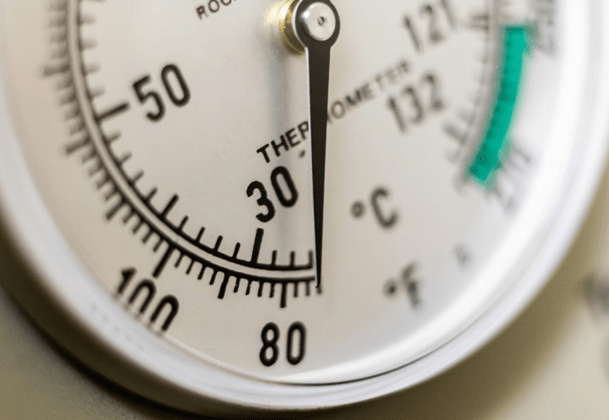
when Choosing CEMS , the accuracy and reliability of the on-site environment must be considered. Factors such as chemicals, high temperatures, and high dust levels can negatively affect the performance of CEMS, as these conditions can cause the system to fail prematurely or provide inaccurate readings. Additionally, CEMS must be able to withstand the extreme weather conditions common in oil and gas facilities, including high winds, lightning, and humidity. The company must choose a CEMS are designed to withstand environmental impacts and provide long-term performance.
In addition to selecting CEMS designed to handle site conditions, companies must also consider how to protect the system from external contaminants. This includes keeping the system away from heavy machinery and other sources of vibration, and ensuring it is installed in a safe location away from corrosive agents. Additionally, it is important to keep the system clean and free of debris, as any dust or dirt can affect the accuracy of the CEMS.
Step 6: Cost and ROI
The cost of the CMES system is a key factor. High-end systems may offer more features, but they may also be more expensive. When selecting a system, carefully weigh required functionality against affordable cost, and consider long-term return on investment (ROI).
CEMS are designed to measure and monitor emissions from industrial processes to ensure compliance with environmental regulations. In addition to the initial purchase cost of a CEMS, the lifetime cost of ownership must also be weighed when selecting. This includes costs associated with installation, calibration, maintenance and repair, as well as costs associated with training personnel to operate and maintain the system. The total lifecycle ownership cost of a CEMS can be significantly higher than the initial purchase cost. Therefore, CEMS options must be carefully evaluated to select the system that provides the most cost-effective solution. Factors such as system reliability, accuracy and ease of use must be considered to ensure long-term value and cost savings. It is worth noting that life cycle costs of ownership can vary significantly depending on the type of system selected and its intended operating environment, so it is important to consider all factors when selecting a CEMS.
Step 7: Training and Support
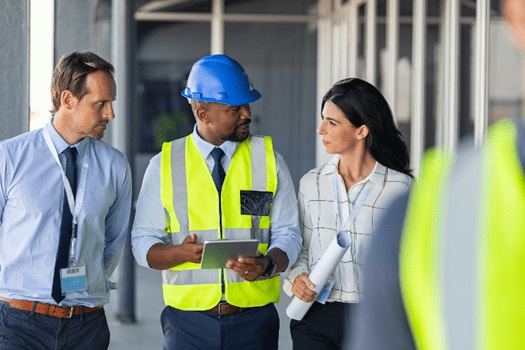
at last, Select supplier Being able to provide training and technical support is important. Ensure your team can get the most out of your chosen CMES system and receive timely support if system issues arise. The selection process requires a thorough analysis of available CEMS technologies, their capabilities, and associated costs. It is important to consider both the upfront and long-term costs of the system and consider maintenance and repair requirements. Additionally, it is important to review the technical support resources available, e.g. Customer support and training, to ensure that the selected CEMS is properly maintained and operated. The selection process should also include an evaluation of the vendor’s customer service and support capabilities to ensure that any technical issues are resolved promptly.
Our CEMS Products
Continuously Emission Monitoring System (CEMS)
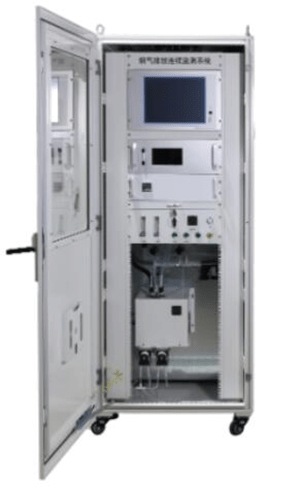
The Continuous Emission Monitoring System (CEMS) EM-GAS-500 developed and produced by ESE is to monitor the total air pollutant emissions from stationary sources, mainly used for industrial boilers, power plant boilers, industrial furnaces emissions monitoring, SO2, NO,NO2, O2,CO,CO2,HCL,HF, H2O etc. dynamic continuous monitoring, simultaneous to measure gas flow, oxygen content, gas pressure, gas temperature, gas humidity etc., automatically recording the total pollutant emissions volume and emission time.
Features:
- The system can automatic sampling, remove dust, calibration, fault diagnosis and alarm.
- System cabinet modular design, simple operation, less maintenance.
- System by heating extraction method for continuous monitoring of flue gas pollutants.
- The sampling probe has big filter area, and filter easy to change.
- The pretreatment device is effectively waterproof and dust proof, anti-corrosion and anti-clogging.
- The stability and reliability of the system are higher by PLC design. System has a variety of data output.
Continuously Emission Monitoring System (CEMS) is a specialized system used to monitor and measure the emissions of pollutants from industrial processes and facilities. It is designed to provide real-time data on the release of pollutants into the environment, helping to ensure compliance with environmental regulations and standards.
CEMS typically consist of several components that work together to measure and monitor emissions. These components may include:
- Gas analyzers: These devices are used to measure the concentration of specific pollutants in the exhaust gases emitted by industrial sources. Common pollutants measured include nitrogen oxides (NOx), sulfur dioxide (SO2), carbon monoxide (CO), particulate matter (PM), and volatile organic compounds (VOCs).
- Sample probes and sample lines: These components are used to extract gas samples from the emission source and transport them to the gas analyzers for analysis. Sample lines are designed to handle the high-temperature and corrosive nature of the gas samples.
- Data acquisition system: This system collects and processes the data from the gas analyzers. It typically includes sensors, transmitters, and data loggers to capture and store the emissions data.
- Calibration systems: To ensure accuracy and reliability, CEMS require periodic calibration. Calibration systems are used to verify and adjust the accuracy of the gas analyzers and other components.
- Data storage and reporting: CEMS generate a significant amount of data, which needs to be stored and analyzed. Data storage systems and software applications are used to store and manage the emissions data. Reporting tools help generate reports and summaries for regulatory compliance and internal tracking.
Conclusion
CEMS play a vital role in environmental monitoring and protection. By continuously monitoring emissions, they help companies identify and control pollution sources, optimize processes to reduce emissions, and ensure compliance with environmental regulations. They also provide valuable data for environmental impact assessments and help develop emission reduction strategies. Choosing a CMES system that suits your gas analysis needs requires considering a number of factors. Identify your needs, choose the right sensing technology, ensure data quality and calibration, consider scalability and integration, carefully weigh cost versus ROI, and select a vendor that provides training and support. By carefully considering these factors, you can select an appropriate CMES system for your gas analysis needs, ensuring your gas emissions monitoring efforts are efficient and accurate while meeting regulatory requirements. I hope this blog has been helpful in your selection process.