Measuring gas flow accurately can be a challenge due to the variability in factors like temperature, pressure, and equipment design. However, precision is essential across industries to maintain safety, efficiency, and regulatory compliance.
Gas flow measurement is achieved by specialized instruments like thermal mass flow meters, differential pressure devices, and turbine meters. These tools, selected based on specific operational needs, account for varying conditions to ensure dependable and accurate readings.
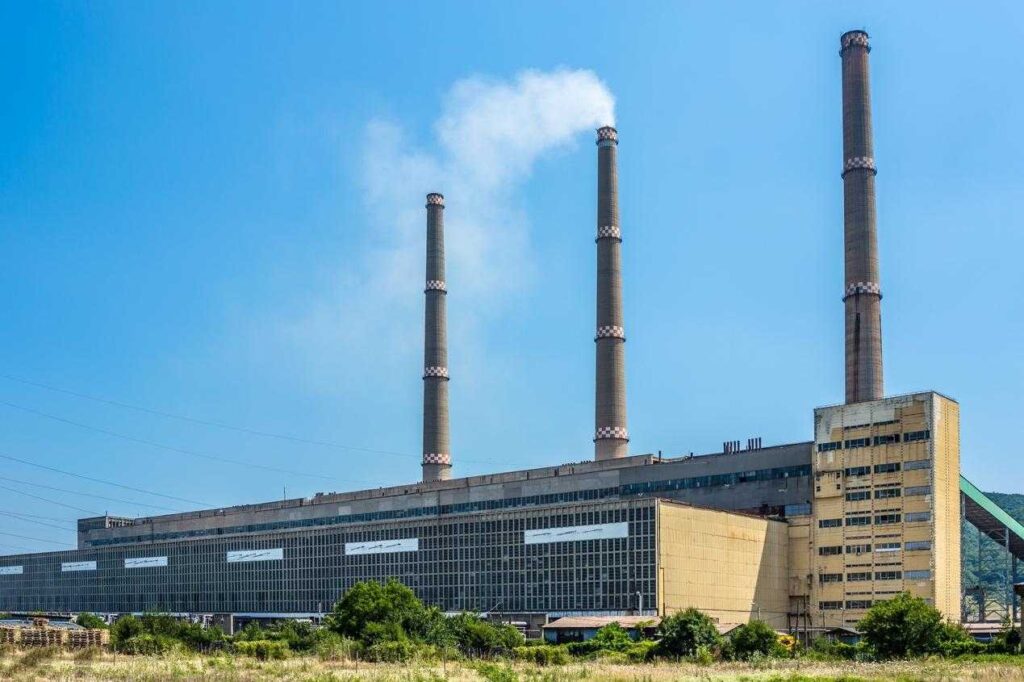
Accurate gas flow measurements support essential processes in industrial, environmental, and commercial applications. This article explores the primary factors that impact measurement accuracy, the methods used, and the technology that supports precise measurement.
What Factors Affect the Accuracy of Gas Flow Measurements?
Various environmental and operational factors significantly impact gas flow accuracy, including temperature, pressure, gas composition, and equipment setup. Gas flow measurement relies on the controlled movement of gas through a system, and changes in these factors can alter readings. For instance, temperature affects the density of gas, which can lead to inaccurate readings if not properly compensated. Pressure changes have a similar effect, as gas molecules compress or expand, altering the flow rate.
The type of gas being measured also matters. Each gas has unique properties, such as molecular weight and viscosity, which influence how it flows through a meter. For example, lighter gases like helium flow differently from denser gases like carbon dioxide, requiring flow meters calibrated for the specific gas type.
Humidity levels are another consideration, particularly in environments with fluctuating moisture. High humidity can affect the gas composition, potentially causing measurement drift if not corrected. Similarly, dirt, particles, and impurities in the gas can clog or interfere with flow meters, impacting their accuracy and reliability.
Selecting the right equipment to account for these variables is crucial. High-performance meters designed for challenging conditions can maintain accuracy even in unstable environments, ensuring reliable data across various applications.
What Are the Most Common Methods for Measuring Gas Flow?
Three widely used gas flow measurement methods are thermal mass, differential pressure, and turbine flow meters, each offering unique benefits and applications.
- Thermal Mass Flow Meters: This method relies on the principle of heat transfer, measuring gas flow by determining the amount of heat lost as the gas passes over a heated sensor. Thermal mass meters are handy for measuring the flow of gases in stable environments, such as in natural gas or biogas applications. They do not require pressure or temperature compensation, making them ideal for certain low-pressure applications. However, these meters may have limitations in rapidly changing temperatures or highly pressurized environments.
- Differential Pressure (DP) Flow Meters: DP flow meters calculate gas flow based on the pressure drop across a constriction, such as an orifice plate or a venturi tube, within the pipe. This type of meter is widely used in industrial applications due to its versatility, as it can be applied across a range of gas types and conditions. However, DP meters typically require pressure and temperature compensation for maximum accuracy, especially in high-temperature or high-pressure settings. These devices are valuable in pipelines or facilities with steady, measurable flows.
- Turbine Flow Meters: Turbine meters measure flow by utilizing the mechanical movement of a rotor within the gas stream. The rotation rate corresponds to the flow rate, making it ideal for monitoring gas with consistent properties in controlled conditions. While turbine meters can provide very accurate measurements for clean, steady flows, they may not be ideal for gases with varying viscosity or particulate contamination, as these factors can lead to rotor wear and reduce accuracy over time.
- Ultrosonic Flow Meter:The Ultrosonic Flow Meter performs gas flow rate measurements by measuring the lag time of ultrasonic pulses; the transmitter/receiver probe is mounted on the side of the flue and is oriented at a certain angle to the direction of gas flow Features Integral two probes,a control and calculation unit,reserved a wealth of interfaces can be expanded to different signal inputs and outputs,can meet the needs of different occasions under the application.
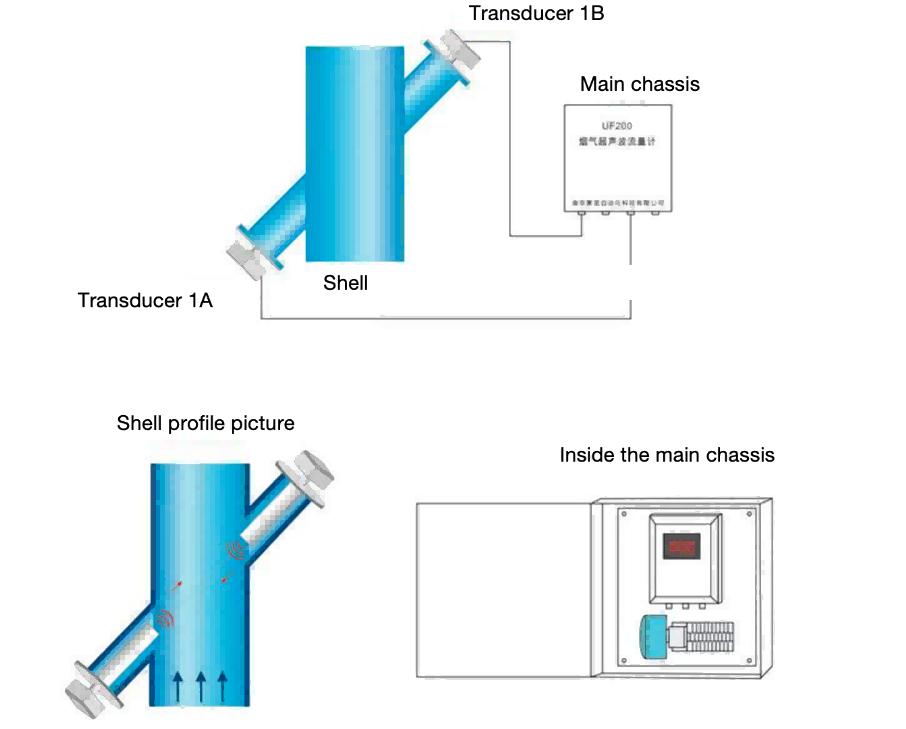
Ultrosonic Flow Meter
Ultrosonic Flow Meter for Flue Gas Application is to measure the flow rate of the gas;it can also calculate and output the volumeflow rate according to the flow rate and the flue size;if you input the temperature and pressure of the flue gas,you can calculate the flow rate under the standard condition.
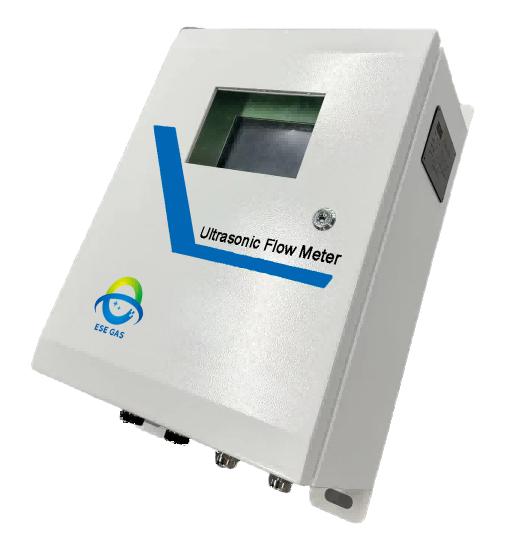
The range of application of the system is as follows:
- Process control engineering
Chemical plants, pharmaceuticals, grain and dairy industry processes.
Plastics processing and refining processes
- Process measurement and emission monitoring
Utility plants, e.g. power plants and boiler emissions.
Waste treatment, e.g. waste incineration plant emissions.
Basic industries, e.g. chemical, iron and steel industries.
- Flow measurement of ventilation, heating and air conditioning systems in agriculture and industry.
Each method has specific advantages, and the selection often depends on the gas composition, flow characteristics, and environmental conditions. Choosing the right flow meter based on these criteria ensures more reliable and precise measurements in various applications.
How Do Ultrasonic Flow Meters Ensure Precision in Gas Measurement?
Ultrasonic flow meters achieve high precision by using sound waves to measure the velocity of gas flow, making them ideal for non-intrusive, high-accuracy applications.
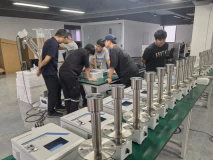
Ultrasonic flow meters work by transmitting sound waves through the gas and analyzing the changes in these waves as they move with or against the gas flow. Typically, two transducers are placed on either side of the pipe. One transducer sends a sound wave that travels along with the flow, while the other sends a wave in the opposite direction. By calculating the time difference between these waves, the meter determines the gas flow velocity, which is then converted to flow rate.
This method offers several advantages for high-precision applications. Since ultrasonic meters are non-intrusive, they do not interfere with the gas flow, which reduces the risk of pressure drops or flow disturbances. They are also highly responsive to changes in flow, providing accurate measurements even with low-velocity gases or in challenging environments.
Ultrasonic flow meters are particularly useful in applications where cleanliness and minimal maintenance are crucial, such as in natural gas distribution, environmental monitoring, and large industrial pipelines. These meters can handle a wide range of gas types and are suitable for both low and high-pressure systems, making them versatile for many industries. However, they may be less effective in conditions with high levels of particulates or moisture, which can interfere with sound wave transmission.
Why Is Calibration Essential for Accurate Gas Flow Measurement?
Regular calibration ensures that gas flow meters maintain their accuracy over time, compensating for factors such as sensor drift, wear, or environmental changes.
Calibration is a critical step in any measurement process. Over time, even the most precise equipment may lose accuracy due to minor wear and sensor aging. Without calibration, small errors can accumulate, leading to significant inaccuracies, especially in industries where precise measurements are crucial for regulatory compliance or safety.
Calibration involves comparing the flow meter’s readings against a known standard and making any necessary adjustments. For example, in facilities that monitor emissions, accurate calibration of gas flow meters is necessary to ensure compliance with environmental regulations. In industrial settings, calibration supports process optimization and quality control by confirming that gas flow remains within specified parameters.
Calibration intervals depend on the application, meter type, and operating conditions. High-precision applications may require more frequent calibrations, while some meters in stable environments can go longer between checks. Either way, establishing a regular calibration schedule is vital to maintaining data reliability and measurement integrity.
What Role Does Technology Play in Enhancing Gas Flow Measurement Accuracy?
New technological advancements, such as digital sensors and automated systems, significantly enhance the accuracy and reliability of gas flow measurements.
Digital technology has transformed gas flow measurement, offering new levels of precision and versatility. Many modern flow meters incorporate digital sensors capable of detecting minute variations in flow, temperature, and pressure. These sensors adjust readings in real time, automatically compensating for environmental changes, which helps reduce human error and enhances measurement consistency.
Additionally, the integration of wireless connectivity allows real-time monitoring and data collection. Operators can access flow data remotely, ensuring they can respond quickly to changes in gas flow, such as unexpected fluctuations in pressure. This is especially valuable in industries like oil and gas, where real-time data supports safety and operational efficiency.
Automated calibration systems are another technological advancement, reducing the downtime typically required for manual calibration. Automated systems also minimize the chance of calibration errors, further supporting measurement accuracy. Together, these advancements help organizations improve efficiency, reduce risks, and maintain compliance with increasingly stringent industry standards.
To learn more about advanced technologies in gas flow measurement, explore Flow Research, which provides insights into current trends and innovations.
Conclusion
Accurate gas flow measurement is essential for safety, compliance, and operational efficiency across various sectors. By understanding the factors that influence measurement, selecting the appropriate methods, and utilizing advanced technology, industries can achieve reliable, precise readings. Regular calibration ensures these measurements remain accurate, supporting critical decision-making in diverse applications.
If you have any questions , welcome to contact us!