energy waste, regulatory risks, and production inefficiencies. Can a precise gas analysis tool solve this?
Infrared gas analyzers offer real-time, high-precision monitoring of critical flue gases in the sintering process, helping steel manufacturers reduce emissions, enhance energy efficiency, and improve process stability.
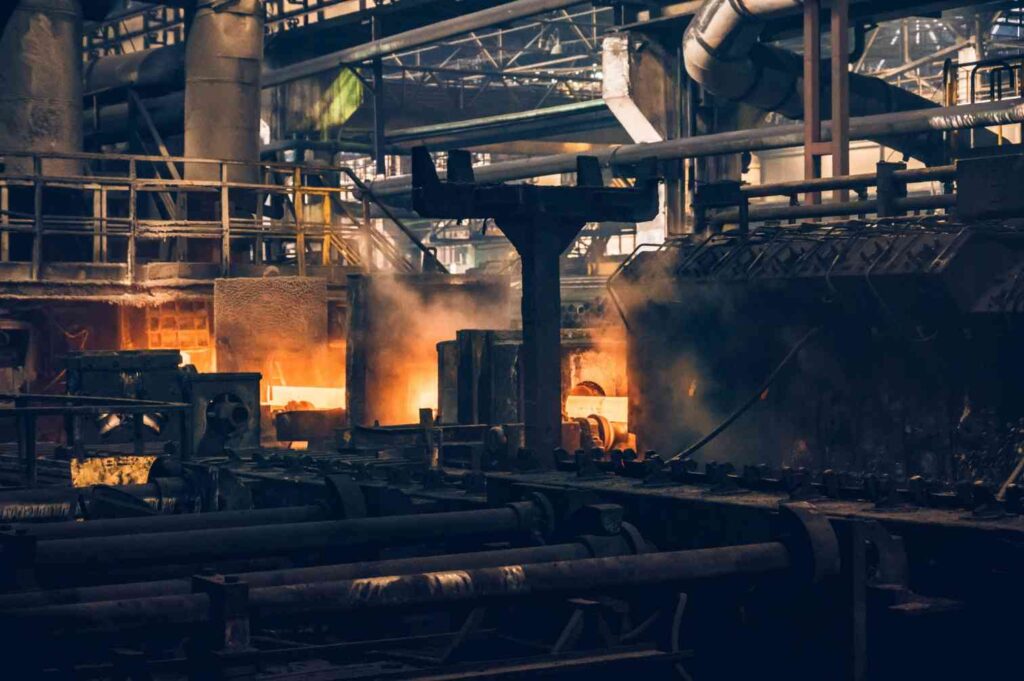
While the environmental and operational benefits are clear, understanding how infrared technology functions within the sintering process reveals its full optimization potential.
Why is Flue Gas Analysis Critical in The Sintering Process Of Steel Production?
Infrared gas analyzers are engineered to detect a range of critical gases that directly impact the efficiency, safety, and environmental footprint of the sintering process in steel production. During sintering, combustion and thermal reactions generate a mixture of process and pollutant gases, each offering key insights into the reaction state and system performance. NDIR (non-dispersive infrared) technology is especially suited for identifying these gases because it measures absorption at specific infrared wavelengths unique to each gas molecule.
Here are the principal gases detected by infrared gas analyzers in the sintering process:
- Carbon Monoxide (CO)
As a product of incomplete combustion, carbon monoxide levels provide immediate feedback on oxygen availability and combustion efficiency. High CO concentrations can indicate an overly rich fuel mixture or poor airflow distribution in the sinter bed. Monitoring CO is essential for process optimization and operator safety.
- Carbon Dioxide (CO₂)
CO₂ is the primary product of complete combustion. Its measurement helps evaluate combustion completeness and fuel utilization efficiency. A stable CO₂ profile typically reflects consistent process conditions and good thermal balance.
- Nitrogen Oxides (NO and NO₂, collectively NOx)
NOx gases form at high temperatures and are tightly regulated due to their environmental impact. Infrared sensors can detect NO directly, while NO₂ is sometimes measured via auxiliary chemiluminescence modules or converted upstream. Monitoring NOx is vital for emissions control and regulatory compliance.
- Sulfur Dioxide (SO₂)
SO₂ is released from sulfur-containing raw materials and fuels. Its concentration varies with material composition and combustion conditions. Continuous SO₂ monitoring ensures adherence to environmental emission limits and helps optimize raw mix selection to reduce sulfur load.
- Water Vapor (H₂O)
Although not always a primary focus, some infrared gas analyzers are equipped to detect water vapor, which affects gas density and can influence the accuracy of dry gas concentration readings. This is particularly useful in compensation algorithms within emission reporting systems.
- Hydrocarbons (HC)
In cases where auxiliary fuels or organic binders are used, trace hydrocarbons may be present. Some advanced IR analyzers can detect total hydrocarbons (THC) as an indicator of unburned fuel or fugitive emissions.
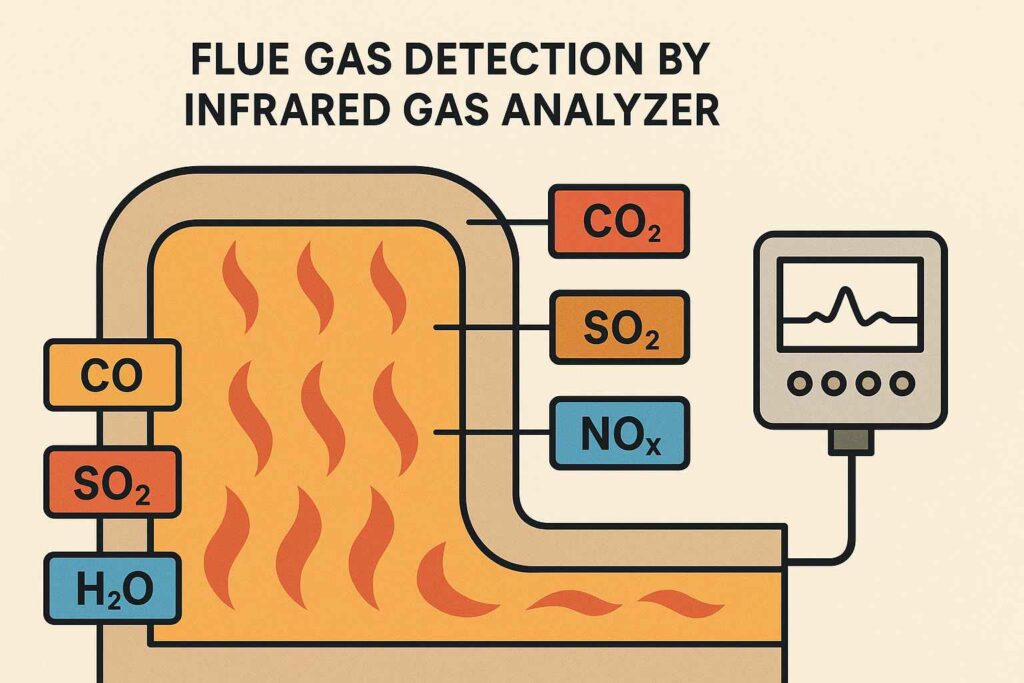
Infrared gas analyzers are preferred in sintering environments due to their non-contact measurement, high selectivity, and fast response time. Unlike electrochemical cells or paramagnetic sensors, IR analyzers are less affected by high temperatures, dust, or corrosive gases, making them ideal for continuous operation in sinter plant exhaust systems.
By delivering high-resolution, gas-specific data, infrared gas analyzers empower operators to make real-time process decisions, optimize energy use, and meet stringent environmental targets—all while minimizing downtime and manual intervention.
How does Real-Time Gas Monitoring Improve Sintering Efficiency and Reduce Emissions?
Real-time gas monitoring fundamentally transforms the sintering process from a reactive operation to a proactive, precision-controlled system. In traditional setups, sintering parameters are adjusted based on time-delayed laboratory results or operator experience, often leading to overcorrection, wasted fuel, and inconsistent sinter quality. By contrast, real-time monitoring using infrared gas analyzers enables minute-by-minute visibility into combustion dynamics, allowing for precise adjustments that directly enhance efficiency and reduce environmental impact.
The sintering process is highly sensitive to oxygen levels, fuel distribution, and combustion zone temperature. Any imbalance can lead to the formation of excessive CO, NOx, or SO₂, reduce sinter bed permeability, or cause uneven sintering—ultimately wasting energy and raw materials. When infrared gas analyzers continuously measure these flue gases, the data can feed directly into an automated control system or alert operators in real-time. This ensures that airflow, burner settings, and raw material feed are optimized dynamically.
For example:
- A sudden rise in CO levels may indicate incomplete combustion. The control system can immediately increase airflow or adjust fuel feed, preventing further inefficiency and limiting CO release.
- Elevated NOx levels can trigger a reduction in peak temperature zones by adjusting burner modulation, helping keep emissions within limits while preserving sinter strength.
- Stable CO₂ trends can confirm optimal combustion, allowing consistent thermal profiles across the sinter bed and minimizing wasted heat.
Moreover, real-time gas data supports process diagnostics. Abnormal gas fluctuations often signal issues like uneven bed layering, clogged suction areas, or faulty burner nozzles—allowing for targeted maintenance before problems escalate into full-scale downtime.
By continuously refining the combustion and heating profile, real-time gas monitoring results in:
- Lower specific fuel consumption
- Improved sinter quality (in terms of strength, reducibility, and porosity)
- Fewer pollutant emissions
- Greater system responsiveness and safety
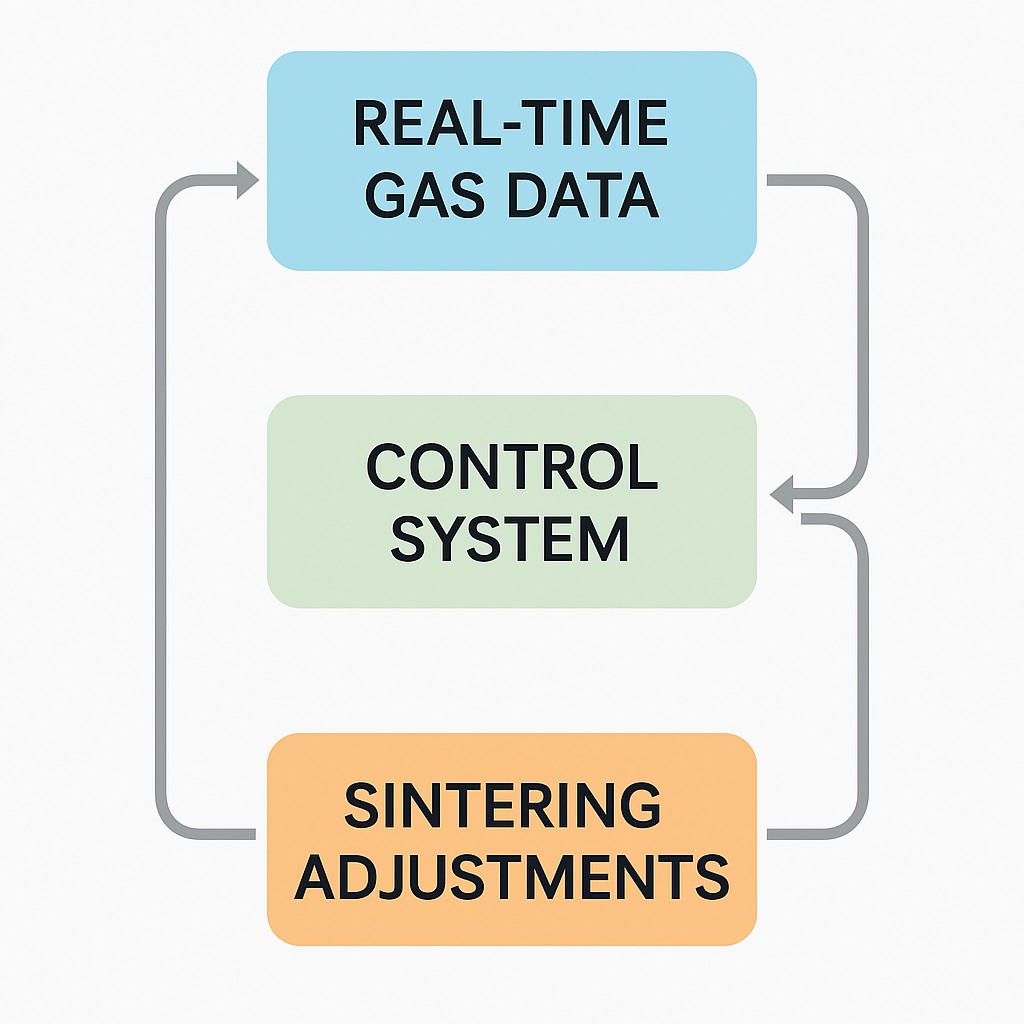
In an industry under growing pressure to decarbonize and meet strict emission targets, the ability to instantly identify and correct inefficiencies is no longer optional—it’s a competitive and regulatory necessity. Real-time gas monitoring is the technological backbone of such a strategy.
How do Infrared Gas Analyzers Support Compliance With Environmental Regulations?
As environmental regulations become increasingly stringent across the globe, steel manufacturers are under growing pressure to precisely monitor, report, and control their emissions, particularly during energy-intensive processes like sintering. Infrared gas analyzers are central in helping facilities meet these obligations by enabling reliable, real-time emissions tracking that aligns with national and international compliance frameworks.
Modern environmental legislation—such as the EU Industrial Emissions Directive (IED), China’s GB standards, or U.S. EPA regulations—requires continuous emissions monitoring systems (CEMS) for pollutants including CO, CO₂, NOx, and SO₂. Infrared gas analyzers, based on non-dispersive infrared (NDIR) technology, are ideally suited for this purpose due to their accuracy, stability, and ability to selectively detect specific gases even in harsh industrial conditions.
Here’s how they specifically support compliance:
- Accurate, Continuous Monitoring (24/7)
Unlike batch sampling or delayed lab analysis, infrared analyzers offer continuous, real-time data. This uninterrupted monitoring ensures that any emissions exceedance is immediately detected and corrected before triggering legal consequences or plant shutdowns.
- High Selectivity and Low Cross-Sensitivity
NDIR analyzers can distinguish between closely related gas species, ensuring that reported values are precise and representative. This is especially important when reporting regulatory thresholds, where even small errors can lead to compliance violations.
- Automated Reporting and Data Logging
Infrared gas analyzers can be integrated with plant-level data acquisition systems to automatically generate reports required by environmental authorities. These reports include time-stamped emission values, trends, and alarms, formatted to meet regulatory submission standards. This not only saves time but ensures traceability and accountability during audits.
- Compliance with Certification Standards
Many infrared gas analyzers are built to meet recognized performance standards such as EN 14181, US EPA 40 CFR Part 60/75, or HJ/T 75-2017 in China. This ensures that the measurement system is legally accepted for official emissions monitoring and reporting.
- Early Warning and Preventive Control
By providing early detection of emission spikes—such as rising NOx or SO₂ levels—infrared analyzers enable preemptive adjustments to burner settings or raw material inputs. This proactive control helps facilities avoid regulatory exceedances and the associated financial and reputational damage.
- Support for ESG and Sustainability Goals
Beyond legal compliance, accurate emissions data from infrared gas analyzers also supports Environmental, Social, and Governance (ESG) reporting. As investors and regulators increasingly demand transparent environmental performance metrics, these analyzers provide the data backbone for credible sustainability disclosures.
What are the Economic And Operational Benefits For Steel Manufacturers Using IR Gas Analyzers?
Infrared (IR) gas analyzers offer more than just regulatory compliance—they serve as strategic assets that generate significant economic and operational advantages for steel manufacturers, especially within the energy-intensive sintering process. By enabling real-time process insight and emissions control, these analyzers help plants save fuel, reduce unplanned downtime, extend equipment lifespan, and enhance overall production stability.
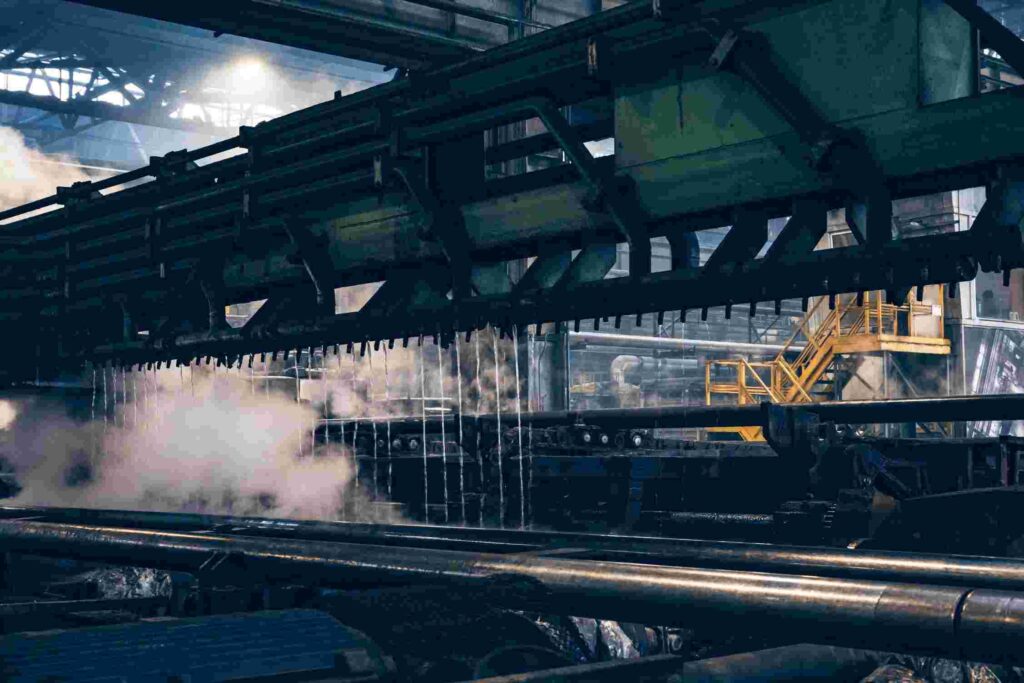
Here’s how these benefits unfold in practice:
1. Fuel Efficiency and Energy Cost Reduction
Precise gas composition data enables operators to optimize the fuel-to-air ratio in real time, minimizing excess oxygen and preventing incomplete combustion. This allows plants to:
- Reduce specific fuel consumption (kg fuel per ton sinter)
- Avoid energy overuse due to conservative, inefficient burner settings
- Balance thermal profiles, preventing hotspots and material waste
In large-scale sinter operations, even a 1–2% gain in combustion efficiency translates to substantial energy cost savings across annual production volumes.
2. Improved Process Stability and Product Quality
Fluctuations in sintering conditions—such as inconsistent bed temperature or airflow—directly affect sinter strength, reducibility, and permeability. IR gas analyzers help detect these variations early by monitoring flue gas changes. With this information, control systems can:
- Maintain consistent sintering zones
- Ensure uniform material bonding
- Reduce rework or scrap due to off-spec sinter
More stable operations mean fewer deviations and less time spent troubleshooting performance issues.
3. Reduced Maintenance and Extended Equipment Life
Uncontrolled combustion conditions lead to excessive wear on suction fans, ducts, and filtration systems due to unburned carbon, corrosive gases, and temperature stress. Infrared gas analyzers help mitigate this by:
- Optimizing combustion for cleaner exhaust gases
- Minimizing corrosive or particulate-laden emissions
- Reducing thermal shock events on refractory linings and metallic components
This proactive control extends the lifespan of key sinter line assets and lowers maintenance frequency and cost.
4. Decreased Downtime Through Predictive Monitoring
Real-time gas trends can reveal early signs of system malfunctions—such as uneven gas distribution indicating bed compaction or CO spikes hinting at burner misfires. With constant data flow, operators can:
- Schedule targeted inspections before failure occurs
- Avoid costly emergency shutdowns
- Run root cause analyses faster with historical emissions data
This predictive approach improves uptime and supports leaner maintenance planning.
5. Enhanced ROI Through Multi-Function Integration
A modern IR gas analyzer is not a single-purpose device—it often integrates with:
- Plant-wide SCADA or DCS systems
- Emissions reporting platforms
- Automated air ratio or burner control loops
This allows the analyzer to play multiple roles—from quality assurance to environmental compliance to energy optimization—all within a single capital investment. As a result, the return on investment (ROI) is realized across multiple departments: operations, maintenance, quality, and sustainability.
In essence, infrared gas analyzers help steel manufacturers produce more with less—less energy, less waste, less downtime, and less risk. They support not only operational excellence but also long-term competitiveness in a market shaped by environmental and economic pressures. Far from being just a sensor, an IR gas analyzer is a powerful enabler of intelligent, efficient steelmaking.
Conclusion
Infrared gas analyzers are transforming sintering operations in steel manufacturing by enabling cleaner emissions, tighter process control, and greater energy efficiency. Their role is pivotal for companies aiming to stay competitive while meeting stringent environmental standards.