Fuel cell production is often hindered by inefficiencies tied to poor gas quality control—ESEGAS syngas analyzers change that with real-time precision monitoring.
Syngas analyzers play a critical role in ensuring gas composition consistency during fuel cell production, significantly improving performance, safety, and system longevity.
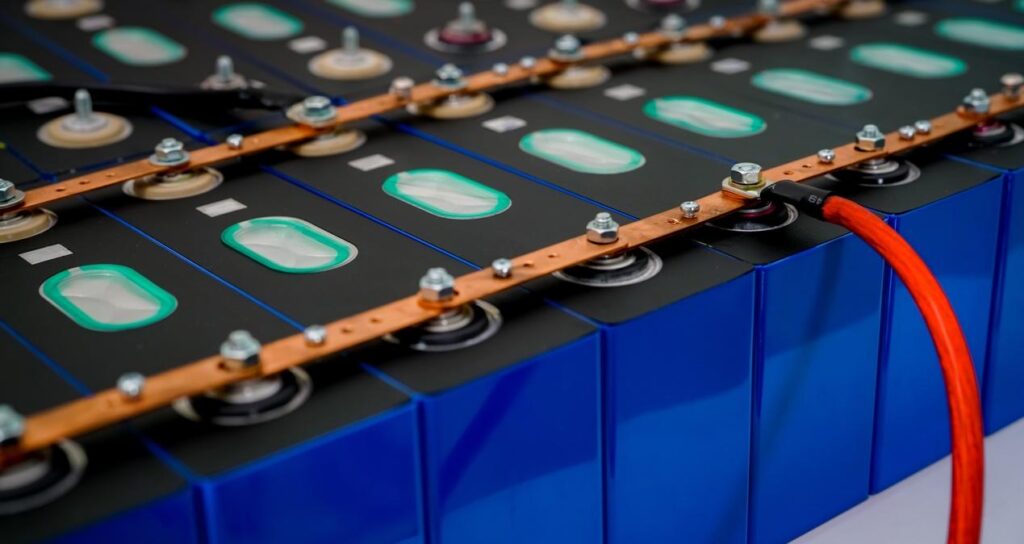
Whether you’re a process engineer or a fuel cell manufacturer, understanding how to enhance gas handling systems is essential. Below, we dive into specific ways syngas analyzers—especially those from ESEGAS—streamline each phase of production.
What role do syngas analyzers play in gas quality control for fuel cell manufacturing?
Inconsistent gas composition leads to unstable reactions—precision analysis is the only cure.
Fuel cell manufacturing relies heavily on the purity and balance of input gases such as hydrogen (H₂), carbon monoxide (CO), carbon dioxide (CO₂), and trace hydrocarbons. Even slight deviations in gas composition can lead to underperformance, catalyst degradation, or structural failures in the cell stack. This makes gas quality control not just a preference, but a fundamental requirement for high-efficiency, low-defect production.
ESEGAS syngas analyzers provide high-resolution, continuous monitoring of syngas components throughout the production line. Unlike batch sampling or off-site lab analysis, ESEGAS instruments offer real-time detection with ppm-level accuracy. This empowers manufacturers to detect contamination, adjust gas blending ratios instantly, and maintain a stable production environment.
Additionally, the analyzers can detect unwanted by-products or inert gases that may compromise electrode reactions or reduce ionic conductivity. By identifying these issues early, ESEGAS analyzers help reduce cell failure rates and extend operational life.
How do syngas analyzers enhance electrode reaction efficiency in fuel cells?
Imbalanced gas ratios sabotage electrode reactions—precision monitoring prevents it at the source.
Electrode efficiency is the heart of fuel cell performance. Whether it’s a Proton Exchange Membrane Fuel Cell (PEMFC) or Solid Oxide Fuel Cell (SOFC), the reaction rate and stability at the anode and cathode directly depend on the precise composition and purity of the syngas mixture.
ESEGAS syngas analyzers play a pivotal role in improving electrode performance through the following mechanisms:
1. Real-Time H₂/CO Ratio Monitoring
Fuel cell electrodes require a specific H₂ to CO ratio to sustain optimal electrochemical reactions. Deviations in this ratio can reduce ion mobility, trigger carbon deposition, or degrade catalysts. ESEGAS analyzers continuously monitor this ratio with high-resolution infrared and thermal conductivity sensors, ensuring consistent fuel delivery to the cell.
2. Impurity Detection to Protect Catalysts
Trace contaminants like sulfur compounds, hydrocarbons, or moisture can poison the electrode catalyst layers, drastically reducing their activity. ESEGAS instruments detect these trace impurities in parts-per-million (ppm) or even parts-per-billion (ppb) levels, allowing for preemptive filtration or process adjustment to protect the cell.
3. Dynamic Adjustment Feedback Loop
Integrated with automated control systems, ESEGAS analyzers feed real-time gas composition data back into the blending or reforming unit. This enables immediate adjustment of feedstock or operational parameters—preventing the slow build-up of inefficient conditions and preserving high electrode throughput.
4. Thermal Stability and Reaction Uniformity
In SOFC systems, inconsistent gas flows or composition can cause localized hot spots, leading to thermal stress on electrodes. By stabilizing syngas quality, ESEGAS analyzers support more uniform thermal distribution and sustained ionic conductivity across the electrolyte-electrode interface.
Technical Challenge | ESEGAS Solution | Performance Benefit |
Unstable H₂/CO Ratio | ✔ Real-time monitoring of H₂/CO via infrared sensors | ✅ Maintains optimal reaction rates at the anode |
Catalyst Poisoning from Trace Impurities | ✔ PPM/PPB-level detection of sulfur, hydrocarbons, and moisture | ✅ Prevents catalyst degradation and extends electrode lifespan |
Slow Process Response to Gas Variations | ✔ Closed-loop feedback to reformers and blending systems | ✅ Enables immediate gas composition correction |
Thermal Hot Spots in SOFC Systems | ✔ Consistent gas delivery ensuring thermal uniformity | ✅ Reduces stress and enhances ionic conductivity |
Production Losses from Gas Fluctuation Events | ✔ Continuous data logging for predictive process control | ✅ Improves yield and prevents off-spec batches |
In short, by delivering constant, precise gas composition data, ESEGAS syngas analyzers ensure the electrode environment remains optimized for high reaction efficiency, longer component life, and consistent power output.
How do syngas analyzers support automation and smart manufacturing in fuel cell systems?
Manual sampling slows down response time—automation demands continuous insight from reliable sensors.
As fuel cell manufacturing evolves toward Industry 4.0 standards, the need for intelligent, self-regulating systems becomes paramount. Traditional approaches that rely on periodic gas sampling and delayed laboratory analysis can no longer meet the demands of modern, high-throughput production environments. In this context, syngas analyzers—particularly those developed by ESEGAS—serve as critical enablers of smart manufacturing by bridging the gap between gas quality control and automated process optimization.
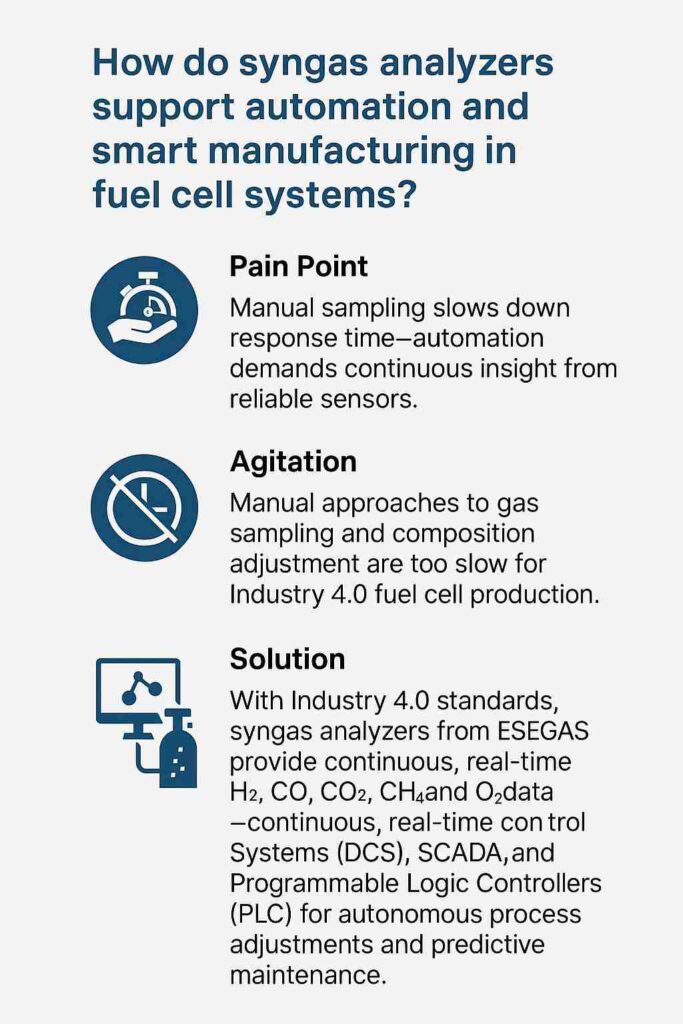
ESEGAS syngas analyzers are equipped with advanced communication protocols such as Modbus TCP/IP, Profibus, and OPC UA, allowing them to seamlessly integrate into Distributed Control Systems (DCS), Supervisory Control and Data Acquisition (SCADA) systems, and Programmable Logic Controllers (PLC). Once integrated, these analyzers provide continuous, real-time data streams on key gas parameters—such as H₂, CO, CO₂, CH₄, and O₂concentrations—allowing the manufacturing system to autonomously respond to any deviation in composition or flow rate.
This closed-loop control capability is vital in processes such as steam methane reforming (SMR) or partial oxidation (POX), where syngas is generated and directly fed into the fuel cell system. If the analyzer detects a shift in the H₂/CO ratio or the emergence of harmful contaminants, the control system can automatically adjust variables like feedstock ratios, reformer temperature, or pressure settings—without human intervention.
In smart manufacturing environments, where production speed, repeatability, and energy efficiency are closely tied to digital integration, the role of the analyzer extends beyond gas measurement—it becomes a real-time decision-making component. By embedding ESEGAS analyzers into the fuel cell production architecture, manufacturers unlock the ability to not only maintain gas quality but also to optimize energy usage, reduce human error, and meet tight regulatory standards with less manual oversight.
Ultimately, syngas analyzers from ESEGAS act as intelligent sensors within an interconnected ecosystem, transforming static gas control into a dynamic, automated, and self-correcting process that elevates the entire fuel cell manufacturing workflow.
How does syngas analysis differ between PEM and SOFC fuel cells?
Assuming one gas strategy fits all leads to failure—different fuel cells demand different analytical precision.
While both Proton Exchange Membrane Fuel Cells (PEMFCs) and Solid Oxide Fuel Cells (SOFCs) rely on syngas as a fuel source, the differences in their operating principles, materials, and temperature ranges mean that their requirements for gas composition, purity, and contaminants vary significantly. Failing to adapt the syngas analysis strategy to each cell type can result in underperformance, material degradation, or system failure.
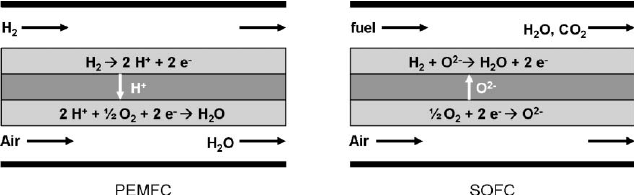
ESEGAS syngas analyzers are engineered with modular sensor platforms and configurable ranges, enabling them to be calibrated for the unique demands of each fuel cell type:
1. PEM Fuel Cells (Proton Exchange Membrane)
- Operating Temperature: ~60–80°C
- Gas Purity Requirement: Extremely high—particularly for hydrogen. PEM cells are highly sensitive to contaminants like CO, H₂S, and NH₃.
- Analytical Focus:
- Detect CO concentrations <10 ppm to avoid catalyst poisoning
- Monitor H₂ purity at 99.999%+ levels
- Flag trace O₂ or moisture that can impact membrane conductivity
- ESEGAS Solution:
- High-sensitivity infrared and electrochemical sensors
- Ultra-low detection limits (ppb to low ppm)
- Moisture compensation and automated zero-drift calibration for continuous accuracy
2. SOFC Fuel Cells (Solid Oxide)
- Operating Temperature: ~600–1000°C
- Gas Flexibility: More tolerant to gas mixtures including CO, CH₄, H₂, and even hydrocarbons
- Analytical Focus:
- Monitor H₂/CO ratio for fuel reformation
- Track CH₄ content and reforming efficiency
- Manage inert gases like CO₂ or N₂ that impact thermal balance
- ESEGAS Solution:
- Wide-range thermal conductivity detectors and NDIR sensors
- High-temperature-compatible gas sampling systems
- Real-time response to changes in reforming dynamics or fuel utilization
This distinction is critical in hybrid or multi-stack fuel cell systems where both PEM and SOFC units might coexist or switch modes based on load demand. Without analyzers that can adapt to these operational differences, gas management becomes inefficient and potentially hazardous.
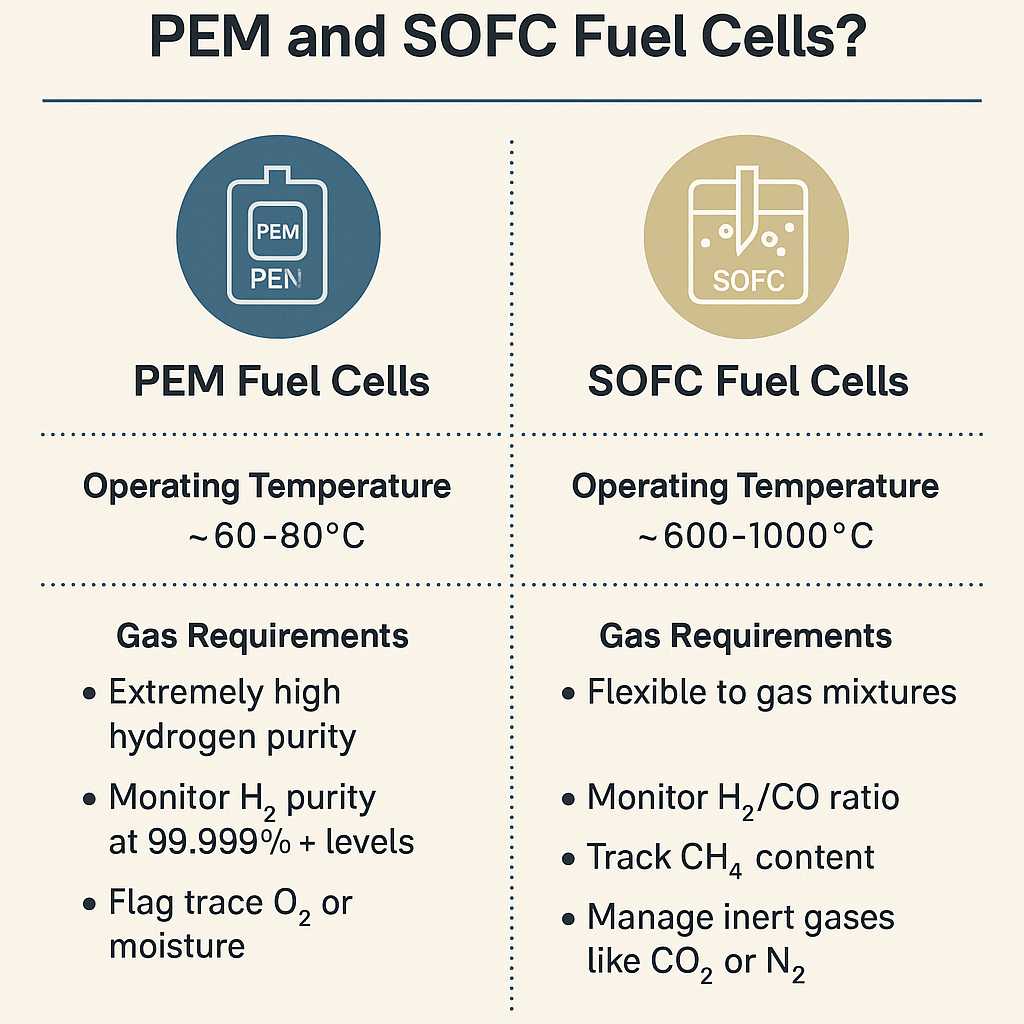
With its scalable architecture, ESEGAS delivers syngas analysis solutions that are not only chemically precise but also adaptable to the operational philosophy of each fuel cell type—ensuring safe, efficient, and optimized performance across the board.
Can using syngas analyzers reduce fuel cell production costs?
Wasted fuel, rework, and downtime quietly drain profits—real-time gas analysis turns these losses into savings.
Fuel cell production is a complex, high-precision process where gas quality directly affects both yield and cost structure. Variations in syngas composition—such as a shift in hydrogen purity, CO levels, or trace contaminants—can lead to suboptimal reactions, poor-quality cells, and equipment degradation. These issues often go undetected in manual or batch-sampling systems, resulting in high scrap rates, unplanned maintenance, and excess use of corrective materials.
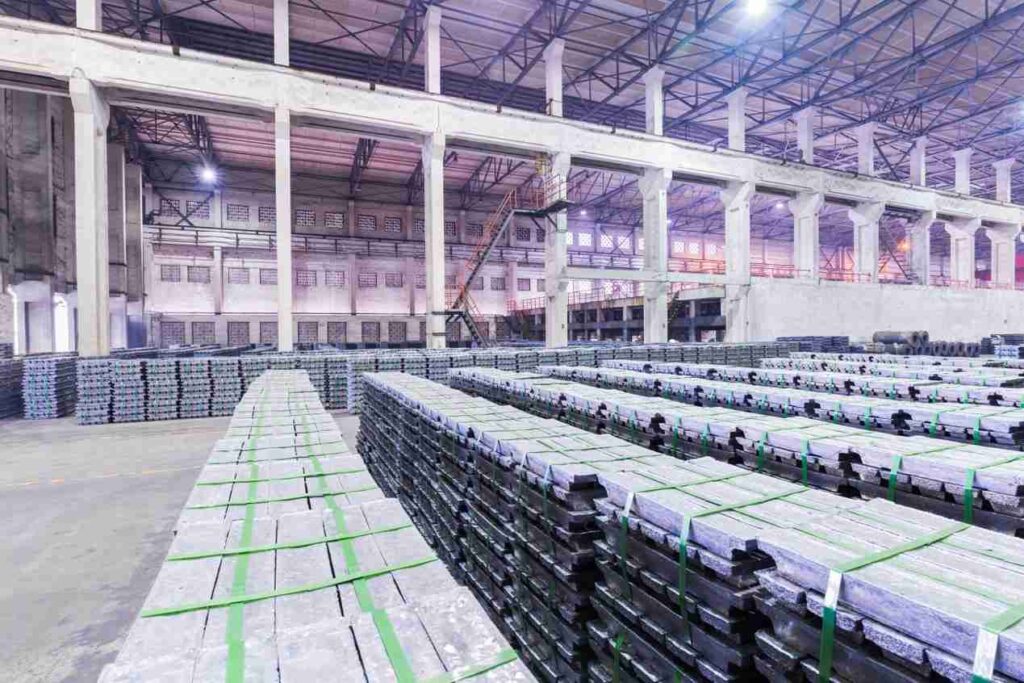
By integrating ESEGAS syngas analyzers into the fuel cell production line, manufacturers gain the ability to monitor critical gas parameters continuously and in real time. This proactive insight allows for immediate correction of deviations in fuel composition before they impact production. For example, if hydrogen purity falls below the specified 99.999% threshold or CO rises beyond tolerance, the system can automatically trigger alerts or even adjust upstream reformer conditions to restore compliance—preventing costly damage to sensitive electrodes and membranes.
Moreover, syngas analyzers from ESEGAS support long-term process optimization through historical trend data and advanced diagnostics. Over time, this data enables manufacturers to fine-tune gas blending strategies, identify energy losses, and improve process stability—all of which contribute to reduced raw material usage and lower energy consumption. In automated environments, analyzers also reduce the need for manual gas testing and operator intervention, further cutting labor costs and minimizing the risk of human error.
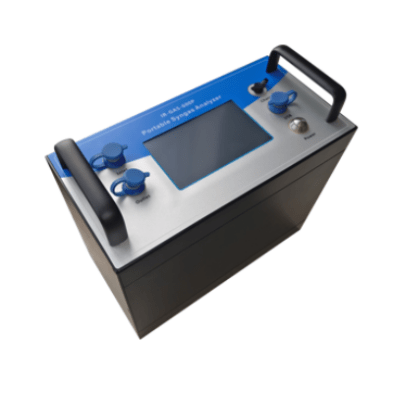
In short, ESEGAS syngas analyzers act as cost-saving instruments by minimizing waste, extending component life, reducing downtime, and enabling precision-driven fuel cell production. The result is a leaner, more efficient operation with faster ROI and improved product consistency.
Conclusion
ESEGAS syngas analyzers play a vital role in improving fuel cell production through real-time monitoring, smart automation, and cost control—ensuring cleaner, more efficient, and scalable energy solutions.
If you have any questions, please contact us and we will get back to you as soon as possible.