After ESEGAS training, our overseas client independently installed four LX‑4000 CEMS units at a major steel plant. They monitored SO₂, NOₓ, CO, CO₂, O₂, humidity, flow rate, and temperature in real time. This success marks a milestone in international cooperation and local technical empowerment.
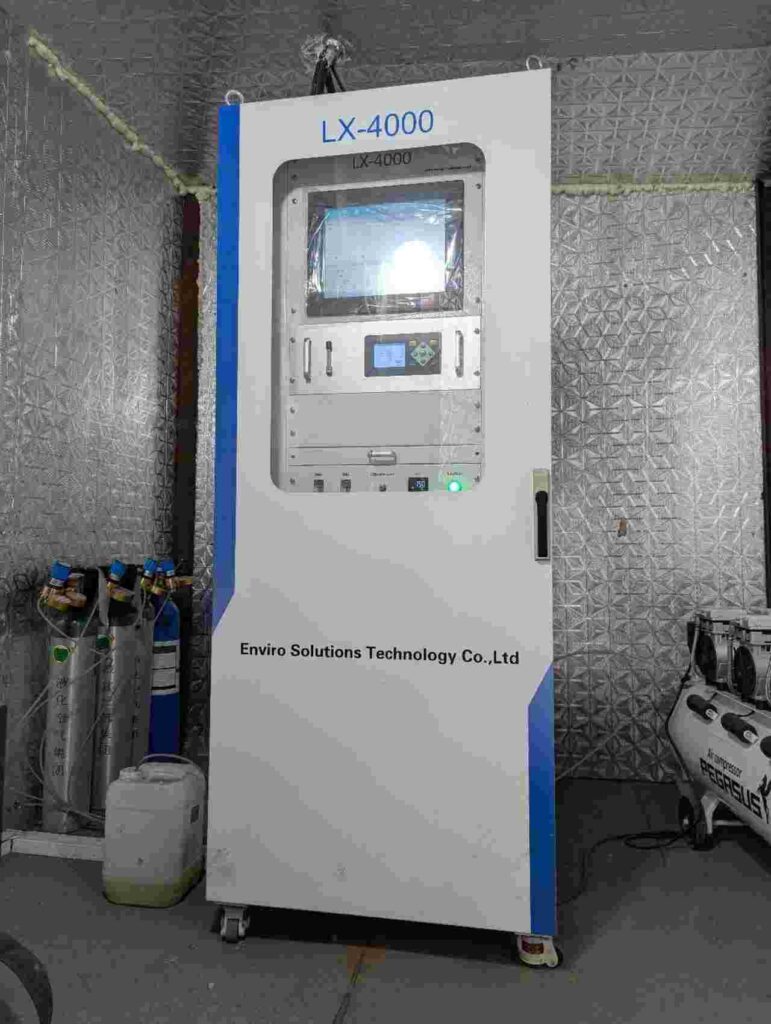
ESEGAS delivered a tailored training program that combined theory and hands‑on sessions.
- First, the team in steel plant studied CEMS architecture and calibration routines.
- Next, they practiced installation with sampling probe, dust monitor, and pitot tube flow meter.
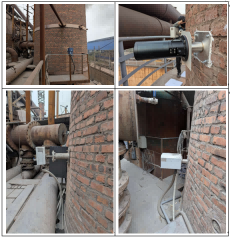
- Then, they continue to practice filter replacement and PLC programming.
- Finally, our experts guided them through troubleshooting, ensuring each engineer felt confident with the system.
Thanks to the CEMS modular design, the customer rolled up their sleeves and assembled four systems in under a week. They connected gas analyzers, sample lines, and data loggers with ease. In addition, the heating‑extraction modules ensured reliable flue gas sampling. Automatic sampling and built‑in alarms simplified commissioning.
After activation, the client observed stable pollutant readings and consistent data logging. The system’s zero and span drift stayed within ±2%FS over seven days. As a result, the steel mill achieved regulatory compliance and improved process control. The client praised ESEGAS’ support and user-friendly design.
Looking ahead, local self‑reliance will drive smarter plant operations. By mastering CEMS technology, our client will fine‑tune processes, optimize fuel usage and meet stricter emission rules. In addition, they stand ready for future expansions.
We’re proud of this achievement and excited to support more partners worldwide. If you seek robust CEMS solutions and hands‑on training, ESEGAS stands ready to help. Contact us to learn more.